Unveiling the Intricacies of Gears: A Journey Through Their Diverse Applications
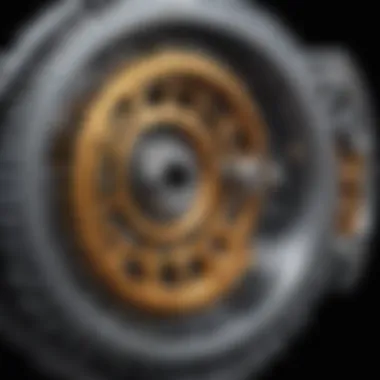
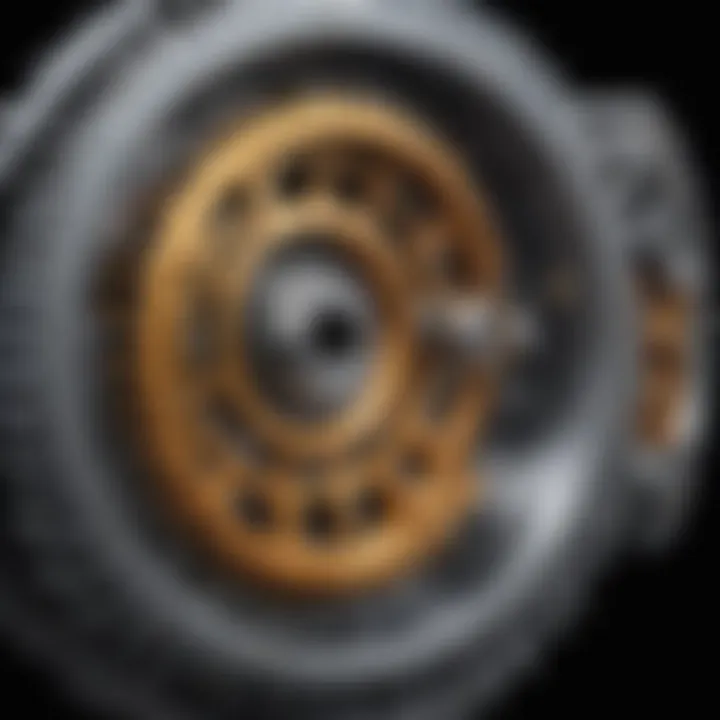
Science Fun Facts
When it comes to the world of gears, there are fascinating details that might surprise you. Did you know that gears have been in use for centuries, dating back to ancient civilizations? These intricate components play a crucial role in the functioning of everything from simple machines to complex industrial equipment. From the gears in old-fashioned clocks to the advanced gear systems in modern vehicles, the history and evolution of gears are truly captivating. Exploring the science behind gears reveals a world of precision engineering and mechanical ingenuity.
Gears are not just about mechanical efficiency; they also have intriguing properties that make them essential in various applications. For example, the shape of gear teeth and the way they interlock determine the speed and power transmission capabilities of a gear system. The design and arrangement of gears can multiply or reduce rotational speed, enabling machinery to perform specific tasks accurately and efficiently. Understanding these underlying principles can help us appreciate the significance of gears in everyday mechanisms and technological innovations.
Delving deeper into the world of gears uncovers a realm of mathematical precision and scientific principles. The relationships between gear sizes, tooth configurations, and rotational speeds are governed by intricate calculations and formulas. Engineers and technicians rely on this mathematical foundation to design gear systems that meet specific performance requirements. By exploring the science behind gears, we gain insight into the complex interplay of forces and motions that drive various mechanical systems and industrial processes.
Discover the Wonders of Science
As we delve into the applications of gears across industries, we unveil a tapestry of innovation and advancement. The omnipresence of gears in machinery, vehicles, and even household appliances underscores their critical role in modern technology. By understanding how gears work and their diverse applications, we open a gateway to exploring the wonders of science and engineering.
From the gears that power elevators to those that drive conveyor belts in factories, the practical implications of gear mechanisms are widespread. Gears contribute to the smooth functioning of intricate systems, ensuring precision and reliability in operations. By examining real-life examples of gear applications, we can appreciate the synergy between technology and engineering that drives progress and efficiency in various sectors.
Education is a key aspect of unlocking the mysteries of gears and their applications. Through interactive learning tools and educational resources, students and enthusiasts can grasp the fundamental concepts of gears and their significance in industrial processes. Visual aids such as animations and videos enhance the learning experience, making complex engineering principles more accessible and engaging. By immersing ourselves in the practical aspects of gear technology, we expand our knowledge of how gears shape the world around us.
Science Experiment Showcase
To truly comprehend the intricacies of gears, engaging in hands-on experiments can offer valuable insights. By following step-by-step instructions and conducting experiments with gear systems, participants can witness the principles of mechanical motion firsthand. From building gear models to studying gear ratios and efficiencies, hands-on experiments bring the science of gears to life.
Safety is paramount when conducting gear experiments, as moving parts and mechanisms require careful handling and supervision. By adhering to safety tips and precautions, participants can enjoy informative and exciting experiments while prioritizing their well-being. The materials list for gear experiments includes items such as gears, axles, and gear assemblies, providing the necessary components to explore gear mechanics in a practical and interactive manner.
Introduction to Gears
Gears, an essential component in mechanical systems, play a crucial role in transmitting motion, power, and torque. They are pivotal in maintaining the direction of rotation, thereby influencing the speed and efficiency of machinery. This section delves into the fundamental aspects of gears, exploring their intricate functions and applications in various industries. Understanding the definition and function of gears is imperative to grasp their significance in driving innovation and enhancing operational precision. By unraveling the complexities of gears, readers will develop a comprehensive insight into their diverse utility and versatile nature.
Definition and Function of Gears
Transmitting Motion and Power
Gears excel in transmitting motion and power efficiently from one component to another within a mechanical system. By interlocking teeth on different gears, they transfer rotational energy, enabling the seamless operation of machinery. This efficient transfer mechanism enhances the overall performance and functionality of various mechanical systems. The precise engagement of gear teeth ensures a reliable power transmission process, contributing to increased efficiency and reduced energy loss in mechanical operations.
Changing Speed and Torque
One of the key functions of gears is their ability to change speed and torque within a mechanical system. By altering the size and arrangement of gear teeth, gears can modify the rotational speed and force applied to different components. This flexibility in adjusting speed and torque levels allows for optimum performance customization based on specific operational requirements. Gears serve as versatile components that facilitate the adaptation of mechanical systems to varying speed and torque conditions, enhancing overall efficiency and operational control.
Maintaining Direction of Rotation
Gears are adept at maintaining the direction of rotation in mechanical systems, ensuring the coordinated movement of interconnected components. The precise alignment of gear teeth prevents reversals or erratic rotations, preserving the intended direction of motion. This feature is crucial in applications where consistent and controlled rotational movement is essential for proper functionality. By upholding the direction of rotation, gears contribute to the stability and predictability of mechanical operations, enhancing the reliability and safety of diverse industrial processes.
Types of Gears
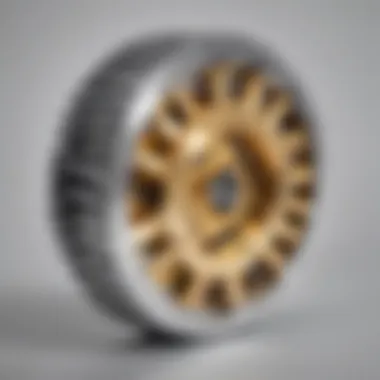
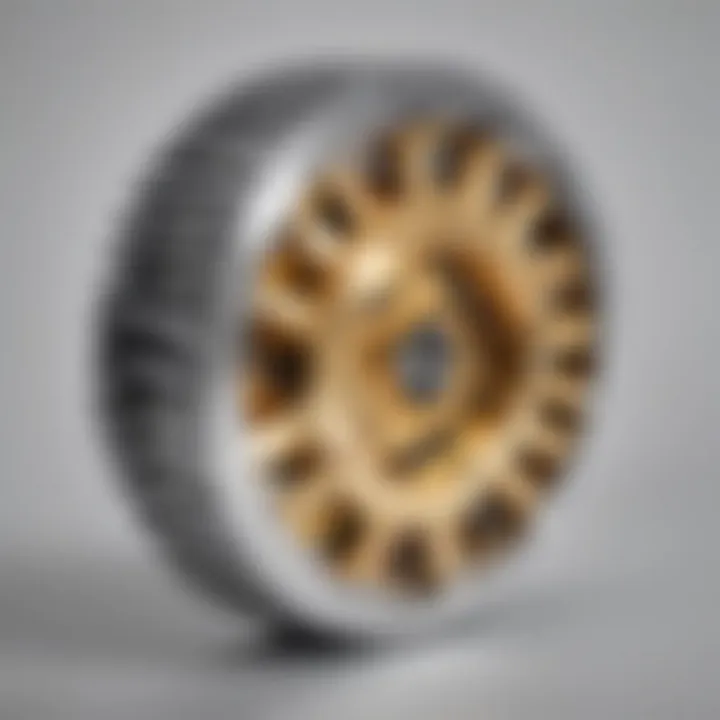
Spur Gears
Spur gears are renowned for their simplicity and effectiveness in transmitting motion in a straight line between parallel shafts. Their straight teeth engage seamlessly, providing smooth and efficient power transmission. The simplicity of design and ease of manufacturing make spur gears a popular choice in various mechanical applications. However, their design limits them to applications that require low to moderate speeds due to higher noise levels and risks of backlash.
Helical Gears
Helical gears feature angled teeth that offer smoother and quieter operation compared to spur gears. The helix angle allows gradual engagement of teeth, resulting in reduced noise levels and smoother transmission of motion. This design enables helical gears to handle higher loads and speeds more effectively, making them suitable for applications requiring precision and reliability. Despite their enhanced performance characteristics, the helical gear design is more complex, requiring careful alignment to prevent thrust forces and ensure optimal operation.
Bevel Gears
Bevel gears are versatile gears used to transmit motion between intersecting shafts at various angles. Their conical shape and tapered teeth enable efficient power transfer between shafts positioned at different orientations. Bevel gears excel in applications where changes in shaft direction are required, such as in automotive differential systems and hand drills. Their versatility and ability to adapt to diverse shaft arrangements make them essential components in mechanical systems that require angular power transmission.
Worm Gears
Worm gears consist of a screw-like gear and a toothed wheel, offering high gear ratios and smooth power transmission at right angles. The unique helical shape of the worm gear allows for significant speed reduction without compromising efficiency. This design feature makes worm gears ideal for applications that demand precise control and high torque output, such as conveyor systems and lifting mechanisms. Despite their advantages in torque multiplication, worm gears are prone to higher friction and lower efficiency compared to other gear types.
Rack and Pinion Gears
Rack and pinion gears combine a linear motion component (rack) with a rotating gear (pinion) to convert rotational motion into linear movement. This gear configuration is commonly used in steering systems, elevators, and CNC machines to facilitate precise and controlled linear motion. The simplicity of the rack and pinion design, coupled with its high mechanical efficiency, makes it a popular choice in applications that require accurate and smooth linear operations. However, alignment and wear issues can affect the long-term performance of rack and pinion gears, necessitating regular maintenance and monitoring to ensure optimal functioning.
Industrial Applications
Gears play a crucial role in various industries, serving as essential components that facilitate the seamless operation of machinery and mechanisms. In the industrial sector, gears are utilized in a myriad of applications, ranging from enhancing operational efficiency to enabling precise control over mechanical systems. Their versatility and reliability make them indispensable in a wide array of operations, contributing significantly to the overall functionality and productivity of industrial processes.
Automotive Industry
Transmission Systems
Transmission systems in the automotive industry are pivotal components responsible for transferring power from the engine to the wheels, allowing the vehicle to change speed and direction efficiently. The key characteristic of transmission systems lies in their ability to modulate torque and speed based on driving conditions, optimizing fuel efficiency and performance. A notable advantage of transmission systems is their adaptability to diverse driving environments, ensuring a smooth driving experience across different terrains. However, one disadvantage is the complexity of modern transmission systems, which may require specialized maintenance and repair services.
Engine Mechanisms
Engine mechanisms, such as camshafts and crankshafts, are integral to the operation of internal combustion engines in vehicles. They control the timing and duration of the engine's intake, compression, power, and exhaust strokes, ensuring optimal combustion efficiency. The key characteristic of engine mechanisms is their precision in synchronizing engine functions, leading to enhanced performance and fuel economy. An advantage of engine mechanisms is their durability and resilience under high operating temperatures, contributing to the longevity of the vehicle's powertrain. Despite their benefits, engine mechanisms can be intricate and costly to replace or repair in case of mechanical failures.
Steering Mechanisms
Steering mechanisms are vital for controlling the direction of a vehicle, allowing drivers to navigate safely and efficiently on the road. The key characteristic of steering mechanisms is their responsiveness and precision in translating steering input into directional changes. This responsiveness enhances overall vehicle handling and maneuverability, ensuring driver safety and comfort. A notable advantage of steering mechanisms is their versatility in accommodating various vehicle designs and sizes, offering compatible solutions for different automotive applications. However, a potential drawback is the complexity of advanced steering systems, which may require calibration and maintenance by trained professionals.
Aerospace Industry
Landing Gear Systems
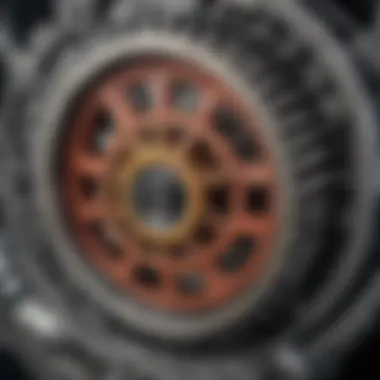
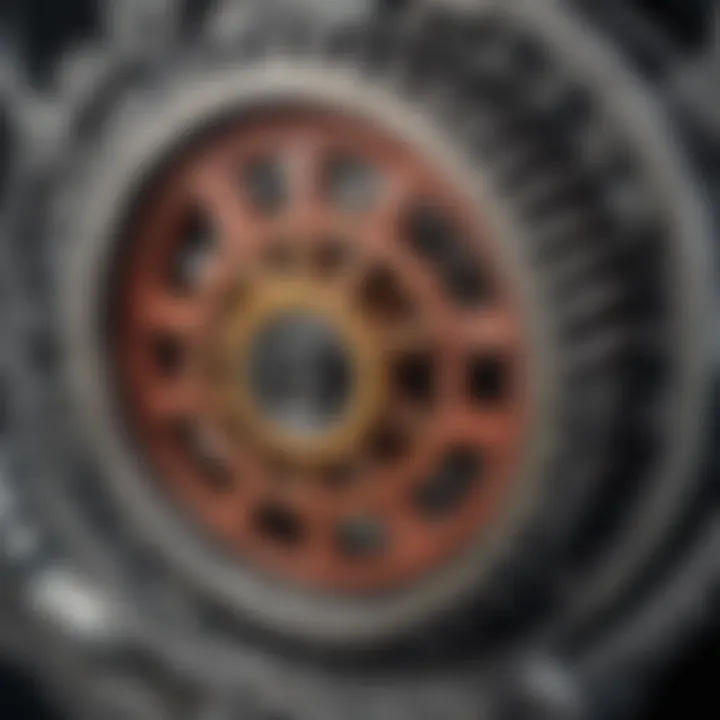
Landing gear systems in the aerospace industry comprise the undercarriage components that support an aircraft during landing and ground operations. The key characteristic of landing gear systems is their robust construction and shock-absorbing capabilities, ensuring smooth landings and taxiing. This feature is essential for optimizing passenger comfort and aircraft structural integrity. An advantage of landing gear systems is their retractable design, which minimizes aerodynamic drag during flight, contributing to fuel efficiency. However, a limitation of landing gear systems is their weight and space requirements, which can impact aircraft payload capacity.
Aircraft Control Devices
Aircraft control devices, including ailerons and rudders, are instrumental in maneuvering an aircraft during flight. They operate by adjusting the aerodynamic forces acting on the aircraft, enabling stable and precise control in different flight phases. The key characteristic of aircraft control devices is their responsiveness to pilot commands, facilitating dynamic adjustments in altitude, direction, and speed. This responsiveness enhances flight safety and efficiency, ensuring optimal aerodynamic performance. An advantage of aircraft control devices is their redundancy systems, which provide backup controls in case of primary system failures. However, the complexity of advanced control systems may require continuous monitoring and calibration to maintain optimal performance.
Manufacturing Sector
Assembly Line Machinery
Assembly line machinery is essential in modern manufacturing processes, facilitating the automated assembly of components in a production line. The key characteristic of assembly line machinery is its high-speed operation and precision in repetitive tasks, enhancing productivity and consistency in manufacturing operations. This efficiency is crucial for meeting production targets and quality standards within tight timelines. An advantage of assembly line machinery is its adaptability to diverse product configurations, allowing manufacturers to reconfigure production lines for different products quickly. However, a challenge is the initial investment required for setting up and integrating assembly line machinery, which may impact capital expenditure in the short term.
Robotic Systems
Robotic systems are revolutionizing the manufacturing sector by automating complex tasks that require precision and agility. These systems utilize robotic arms and end effectors to perform intricate operations, such as welding, painting, and assembly. The key characteristic of robotic systems is their programmability and versatility in adapting to evolving production demands, reducing human intervention and labor costs. This flexibility enables manufacturers to optimize workflow efficiency and product quality while ensuring worker safety. An advantage of robotic systems is their continuous operation capabilities, allowing for 247 production cycles without fatigue or errors. However, the high maintenance costs and initial setup investment can be significant drawbacks for smaller manufacturing facilities.
Packaging Equipment
Packaging equipment plays a vital role in the final stage of manufacturing, where products are prepared for distribution and sale. These machines automate the packaging process, including filling, sealing, labeling, and palletizing, ensuring product safety and presentation standards. The key characteristic of packaging equipment is its efficiency in handling various packaging materials and formats, reducing packaging time and minimizing wastage. This efficiency streamlines the packaging workflow, improving overall logistics and customer satisfaction. An advantage of packaging equipment is its customization options to meet specific packaging requirements, offering tailored solutions for diverse product categories. However, the complexity of advanced packaging machinery may require specialized training for operators, impacting employee skill development and operational consistency.
Technological Innovations
In the vast realm of gears, technological innovations play a crucial role in revolutionizing various industries. These advancements not only enhance the efficiency of machinery but also drive cutting-edge developments in modern technology. By integrating state-of-the-art robotics and automation systems, industries have been able to streamline processes, reduce manual labor, and improve overall productivity. The seamless integration of technological innovations with gears has paved the way for groundbreaking solutions across different sectors.
Robotics and Automation
Industrial Robots
Industrial robots are a cornerstone of automation, offering precise and efficient operation in manufacturing and industrial settings. These robots are equipped with advanced sensors and programming capabilities, allowing them to perform complex tasks with accuracy and speed. The key characteristic of industrial robots lies in their versatility, as they can be programmed to handle a wide range of functions, from assembly to welding. Their ability to work tirelessly without fatigue makes them a popular choice for industries seeking to boost production capacity and maintain consistency in output.
Automated Guided Vehicles
Automated Guided Vehicles (AGVs) are instrumental in optimizing material handling and logistics operations. These vehicles navigate using laser guidance or magnetic tapes, enabling them to transport goods autonomously within a facility. The key characteristic of AGVs is their agility and adaptability in dynamic environments, effortlessly moving payloads from one point to another with precision. Their unique feature lies in their ability to operate without human intervention, reducing the risk of manual errors and enhancing operational efficiency.
Medical Devices
Within the healthcare sector, gears play a vital role in powering advanced medical devices that aid in diagnosis, treatment, and surgery. These technological marvels have revolutionized the field of medicine, offering greater precision, accuracy, and patient outcomes. Surgical robots, for instance, have become indispensable tools in minimally invasive surgery, enabling surgeons to perform complex procedures with enhanced dexterity and minimal invasiveness. Their unique feature of providing a 3D view and articulated movement enhances surgical precision while reducing patient recovery times. On the other hand, diagnostic equipment such as MRI machines and CT scanners rely on gears to deliver precise imaging results, aiding healthcare professionals in detecting and treating a myriad of conditions.
Surgical Robots
Surgical robots are at the forefront of medical technology, enhancing surgical procedures through unparalleled precision and control. The key characteristic of surgical robots is their capability to translate a surgeon's hand movements into precise micro-movements during surgery. This feature not only improves surgical outcomes but also minimizes the risk of human error, making them a popular choice for delicate and intricate procedures. Despite their advantages in terms of accuracy and minimally invasive surgery, the high cost of procurement and maintenance remains a notable drawback of using surgical robots in healthcare settings.
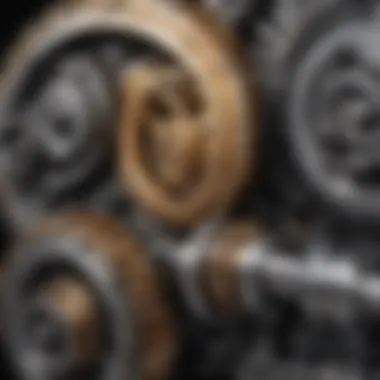
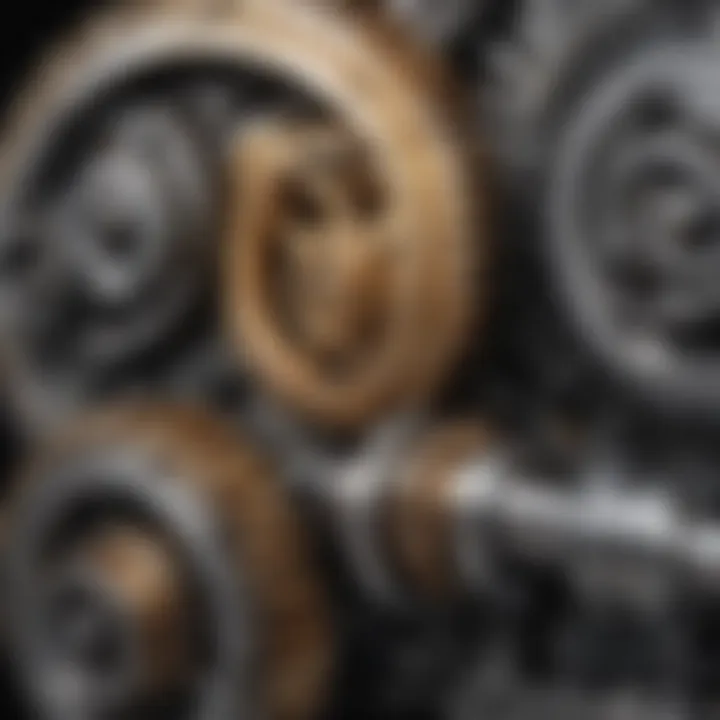
Diagnostic Equipment
Diagnostic equipment plays a critical role in identifying and monitoring various medical conditions, underpinning the diagnostic process in healthcare. The key characteristic of diagnostic equipment lies in its ability to generate detailed images and data for medical analysis. This feature is essential in facilitating early disease detection and providing insights for treatment planning. The unique feature of diagnostic equipment is its non-invasiveness, allowing healthcare professionals to obtain accurate diagnostic information without the need for invasive procedures. However, the high initial investment and periodic maintenance costs pose challenges in adopting and employing advanced diagnostic equipment in healthcare facilities.
Renewable Energy Systems
Renewable energy systems harness the power of nature to generate sustainable energy, with gears playing a fundamental role in optimizing energy production and distribution. From wind turbines to solar tracking systems, these innovations leverage gear technology to maximize energy efficiency and minimize environmental impact. By seamlessly integrating gears into renewable energy systems, industries can enhance power generation capabilities while reducing reliance on fossil fuels.
Wind Turbines
Wind turbines are iconic symbols of renewable energy, utilizing gears to convert wind energy into electricity. The key characteristic of wind turbines is their ability to capture and harness wind power efficiently, generating clean electricity for a wide range of applications. Their unique feature lies in their adaptability to various wind conditions, adjusting rotor speeds to optimize energy output. While wind turbines offer a sustainable energy solution, concerns regarding their visual impact and noise levels have been raised in certain communities.
Solar Tracking Systems
Solar tracking systems are pivotal in maximizing solar energy capture by orienting solar panels towards the sun's position throughout the day. The key characteristic of these systems is their ability to enhance solar energy production by tracking the sun's trajectory and adjusting panel angles accordingly. This feature significantly improves solar panel efficiency, increasing overall energy yields. The unique feature of solar tracking systems lies in their capacity to generate more electricity compared to fixed-tilt installations, making them a preferred choice for commercial and utility-scale solar projects. Despite their advantages in enhancing energy generation, the complexity and maintenance requirements of solar tracking systems may pose operational challenges for some installations.
Everyday Uses
Gears play an essential role in everyday objects that we often take for granted, such as clocks, watches, bicycles, and kitchen appliances. These devices rely on gears to perform specific functions with precision and efficiency. Understanding the significance of gears in these items illuminates how a fundamental mechanical component impacts our daily lives. By exploring the practical applications of gears in clocks, watches, bicycles, and kitchen appliances, we can grasp the intricate ways in which these simple mechanisms enhance functionality and convenience.
Clocks and Watches
Clocks and watches are perfect examples of intricate mechanisms where gears are instrumental. Gears in these timepieces control the movement of hands, ensuring accurate timekeeping. Additionally, gears facilitate the intricate functions of features like alarms and chronographs in watches. In clocks, gears regulate pendulum movements or balance wheels to maintain precise time. The precise interplay of gears in these timekeeping devices showcases the meticulous engineering behind something as ubiquitous as a clock or watch.
Bicycles and Gear Trains
Bicycles are reliant on gear mechanisms to enhance pedal efficiency and speed control. Gear trains in bicycles enable riders to adjust resistance levels when cycling uphill or cruising on flat terrain. The gear ratio determines the relationship between pedaling cadence and wheel rotation, significantly impacting the rider's experience. By exploring the role of gears in bicycles and gear trains, we uncover the mechanical ingenuity that allows cyclists to maneuver various terrains comfortably and efficiently.
Kitchen Appliances
Kitchen appliances like blenders, food processors, and mixers utilize gears to power their blades or beaters effectively. Gears in these appliances transfer rotational energy from the motor to the working components, ensuring efficient food processing or mixing. Additionally, gears in appliances like coffee grinders control grind size and consistency. Understanding the application of gears in kitchen appliances highlights how these components streamline cooking processes and enhance culinary experiences.
Conclusion
Gears play a crucial role in various industries by ensuring the smooth functioning of machinery and mechanisms. Understanding the impact and significance of gears is imperative to appreciate how these simple yet powerful devices shape modern technology. Gears are instrumental in driving technological advancements, enhancing efficiency and precision, and enabling innovative designs, making them indispensable components across industries.
Impact and Significance of Gears
Driving Technological Advancements
Gears drive technological advancements by efficiently transmitting motion and power in various systems. Their ability to change speed and torque while maintaining the direction of rotation is paramount in enhancing the functionality of machinery. Gears offer precision and reliability in operations, making them a popular choice in modern engineering. The unique feature of gears lies in their mechanical advantage, where they amplify input force to achieve desired output, thereby boosting overall system performance.
Enhancing Efficiency and Precision
Gears significantly enhance efficiency and precision in machines by ensuring accurate speed control and power distribution. The teeth configuration of gears allows for smooth engagement and minimal energy wastage during transmission. This characteristic makes gears a beneficial choice in systems where precise movement and power distribution are critical. While gears excel in improving mechanical efficiency, the main disadvantage lies in potential frictional losses and noise generation during operation.
Enabling Innovative Designs
Gears enable the creation of innovative designs by facilitating complex motion mechanisms and system integrations. Their versatility in transferring motion between intersecting or non-parallel shafts opens up new possibilities in machine design. Gears are instrumental in creating compact and functional systems by enabling the transmission of power through small, intricate spaces. The unique feature of gears lies in their adaptability to diverse applications, allowing engineers to craft inventive solutions that maximize performance. However, one potential disadvantage of intricate gear designs is the increased risk of mechanical complexity and maintenance challenges.