Unveiling the Enigmatic World of Line Following Robots
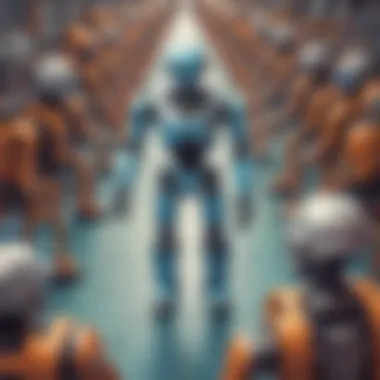
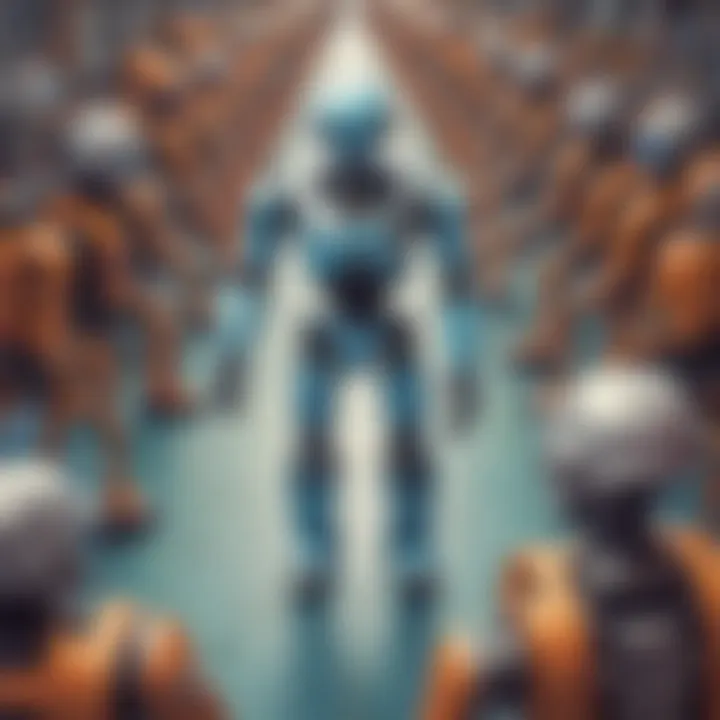
Science Fun Facts
Line following robots, with their precise sensors and intricate programming, can follow paths autonomously with remarkable accuracy, akin to a talented dancer effortlessly gliding across a stage. The innovative technology behind these robots allows them to discern contrasting colors or different light intensities, enabling them to stay on course even in complex environments. What may appear as simple movements involves a complex interplay of sensors, logic, and swift decision-making.
Discover the Wonders of Science
Within the realm of line following robots lies a fusion of art and science, where creativity meets logic to navigate the intricate web of pathways. By exploring the underlying principles of sensor technologies and programming techniques, we unravel a tapestry of innovation that powers these robots' seamless movements. Through educational videos and interactive simulations, we can grasp the practical applications of these robots, from industrial automation to educational tools in schools.
Science Quiz Time
Engage in a playful challenge with interactive quizzes designed to test your understanding of line following robots. Delve into multiple-choice questions that probe your knowledge of sensor functionalities and decision-making algorithms. Unravel brain teasers that prompt critical thinking about the real-world implications of autonomous navigation and the role of robots in shaping our future landscapes.
Science Experiment Showcase
Embark on a hands-on journey with fun and engaging experiments that mirror the principles governing line following robots. Follow step-by-step instructions to build a basic line-following robot using everyday materials, nurturing a curiosity for robotics and automation. Prioritize safety tips and precautions to ensure a seamless and enjoyable experimentation process, fostering a love for scientific exploration from a young age.
Introduction to Line Following Robots
In this detailed exploration of line following robots, we delve into the intricate world of these intelligent machines that effortlessly navigate predefined paths. By understanding the importance of line-following robots in the realm of robotics, we can grasp the fundamental concepts and advancements shaping this field. Highlighting the key points to be discussed in this section will provide a comprehensive overview of the core elements and benefits associated with line following robots.
Understanding the Concept of Line Following Robots
Defining Line Following Robots:
Defining line following robots is crucial to comprehend their functionality within the context of automation. These specialized robots are designed to follow distinct pathways marked by lines, utilizing advanced sensor technologies for guidance. The key characteristic of line following robots lies in their ability to interpret and respond to the signals received from these sensors, making them integral to various applications. Their unique feature of precise path-tracking showcases their efficiency in tasks requiring consistent and accurate movement along designated routes.
Historical Context of Line Following Robots:
Exploring the historical context of line following robots unveils the evolutionary journey of this technology in robotics. From their early developments to modern-day implementations, the historical lineage underscores the innovation and progression within this field. Understanding the roots of line following robots provides valuable insights into the challenges faced and overcome, contributing to their current status as a staple component in robotic systems. Recognizing the advantages and disadvantages stemming from historical perspectives enriches the narrative surrounding these intelligent machines.
Importance of Line Following Robots in Robotics
Role in Automation:
The role of line following robots in automation signifies their pivotal contribution to streamlining processes and enhancing operational efficiency. By autonomously following predefined paths, these robots reduce manual intervention and increase productivity in various industries. Their key characteristic of precision movement aligns perfectly with the automated requirements of tasks, making them a popular choice for improving workflow dynamics. The unique feature of adaptability to diverse environments underscores their versatility in automation applications.
Applications in Various Industries:
Exploring the applications of line following robots across different industries sheds light on their multifaceted utility and impact. From manufacturing facilities to logistics operations, these robots play a vital role in optimizing processes and ensuring seamless operations. Their key characteristic of adaptability to specific industry requirements makes them a preferred choice for tasks ranging from material handling to quality control. Understanding the advantages and disadvantages in different industrial settings reveals the nuances of deploying line following robots effectively.
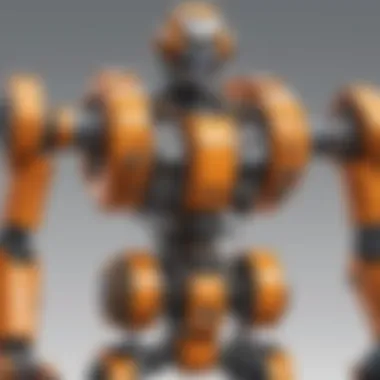
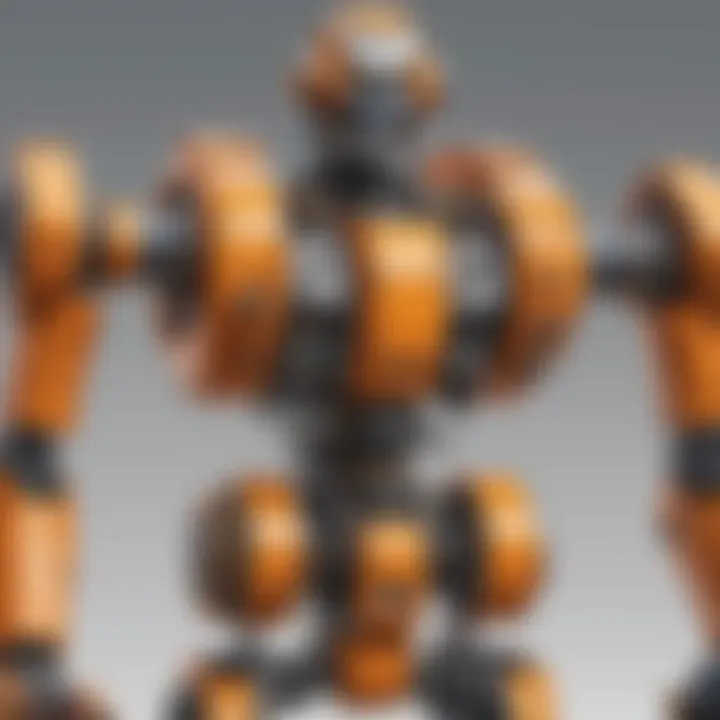
Key Components of Line Following Robots
Sensors:
Sensors serve as the sensory organs of line following robots, enabling them to perceive their surroundings and follow designated paths accurately. The key characteristic of sensors lies in their ability to detect lines, obstacles, and changes in terrain, providing essential data for navigation. With advanced sensor technologies, these robots can make real-time adjustments to ensure optimal performance, demonstrating their reliability in various environments. The unique feature of sensor integration underscores the precision and intelligence embedded in the design of line following robots.
Microcontrollers:
Microcontrollers act as the brain of line following robots, orchestrating the integration of sensor data with navigational algorithms. Their key characteristic of processing information swiftly and making split-second decisions enables seamless operation of these robots. By utilizing efficient microcontrollers, these robots can respond to stimuli promptly, showcasing their agility and responsiveness in dynamic environments. The unique feature of microcontroller programming highlights the importance of tailored algorithms for enhancing the capabilities of line following robots.
Wheels and Motors:
Wheels and motors form the mechanical backbone of line following robots, translating electronic commands into physical movement. The key characteristic of wheels and motors lies in their ability to provide traction and maneuverability on various surfaces, ensuring smooth navigation along predefined paths. With robust wheel configurations and motor systems, these robots can navigate complex terrains with precision, illustrating their reliability in diverse settings. The unique feature of modular wheel and motor designs offers flexibility for customization and optimization based on specific performance requirements.
Design and Functionality of Line Following Robots
In this section of the article, we delve into the crucial aspect of the design and functionality of line following robots. Understanding the intricacies of how these robots are structured and operate is paramount in comprehending their significance in the field of robotics. The design and functionality play a pivotal role in ensuring the smooth navigation and accuracy of these intelligent machines along predefined paths. By exploring the key components, mechanisms, and considerations involved in their design, readers will gain a comprehensive insight into the inner workings of line following robots.
Sensor Technologies in Line Following Robots
Types of Sensors Used
The types of sensors used in line following robots are fundamental to their operation. These sensors serve as the sensory organs of the robot, enabling it to detect and follow the designated path consistently. Among the various types of sensors employed, infrared sensors are particularly prevalent for their accuracy in line detection and cost-effectiveness. Their ability to distinguish between different surfaces based on their reflectivity makes them a popular choice for line following applications. Despite their effectiveness, one downside of infrared sensors is their susceptibility to ambient light interference, which can affect their performance in certain conditions.
Working Principle of Sensors
The working principle of sensors in line following robots revolves around their ability to detect the contrast between the path and its surroundings. By emitting infrared light and measuring its reflection off the surface, these sensors can identify the path and make real-time adjustments to stay on course. This principle of reflection and detection forms the core functionality of sensors in guiding the robot along the desired route. While this method offers accuracy and speed in navigation, variations in surface color and texture can pose challenges to sensor reliability.
Navigation Techniques Implemented
PID Control
PID control, or Proportional-Integral-Derivative control, is a paramount navigation technique implemented in line following robots. This control mechanism ensures the robot maintains stability and follows the path with precision by continuously adjusting its position based on error signals. The proportional term guides the robot to move towards the center of the line, while the integral term corrects any accumulated errors, and the derivative term predicts future errors. This technique's effectiveness lies in its ability to maintain a consistent and balanced movement along the path, enhancing the robot's line following accuracy.
Algorithmic Approaches
Algorithmic approaches in line following robots involve the utilization of algorithms to analyze sensor data and make informed navigational decisions. These algorithms leverage data processing techniques to interpret sensor inputs, calculate optimal trajectories, and execute responsive maneuvers. One prevalent approach is the use of decision trees to map out possible paths based on sensor feedback, enabling the robot to choose the most appropriate route. By integrating sophisticated algorithms, line following robots can navigate complex paths efficiently and swiftly.
Chassis Design and Mobility
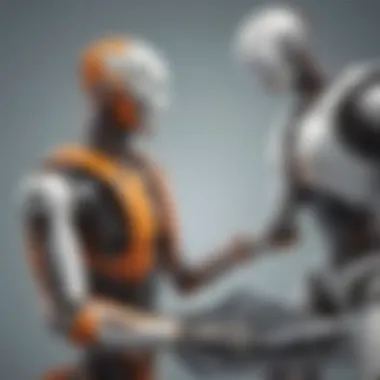
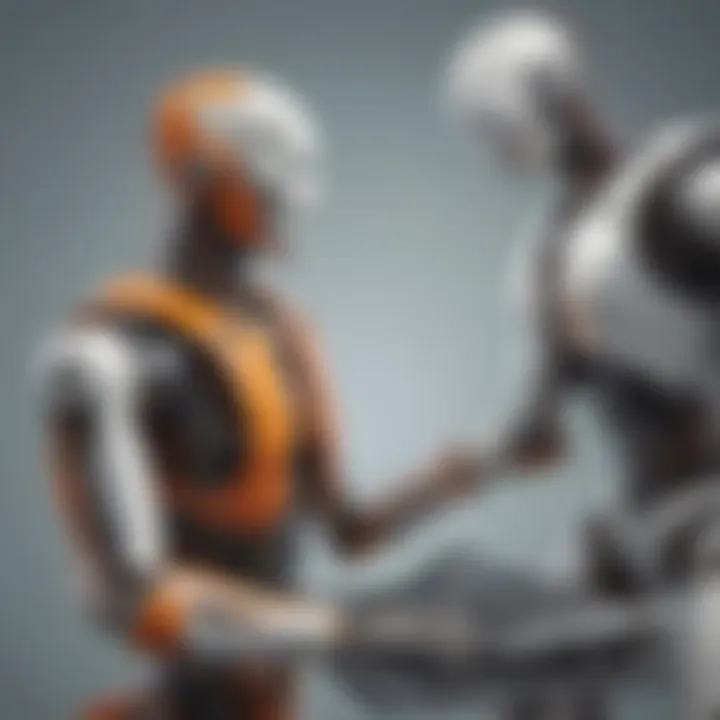
Wheel Configuration
The wheel configuration of line following robots is a critical element that influences their maneuverability and stability during navigation. The choice of wheel arrangement, such as differential drive or omnidirectional wheels, significantly impacts the robot's turning radius and agility. For line following tasks that require sharp turns or precise movements, a differential drive system with two drive wheels offers versatile control and responsiveness. However, omnidirectional wheels provide exceptional agility and maneuverability in crowded or intricate environments, enhancing the robot's adaptability to diverse paths.
Mechanical Structure
The mechanical structure of a line following robot encompasses its physical framework and components that support its functionalities. The construction of a sturdy chassis, durable materials, and efficient weight distribution are paramount in ensuring the robot's durability and performance. By incorporating lightweight yet robust materials and a strategic design that minimizes vibrations and impact, the mechanical structure plays a vital role in optimizing the robot's stability and longevity. Moreover, the integration of precise components such as motors and gears within the mechanical assembly enhances the robot's operational efficiency and accuracy.
Integration of Software and Hardware
Programming Languages
The choice of programming languages in line following robots determines the flexibility and functionality of their control systems. Popular languages such as C++, Python, or Arduino are commonly used to implement algorithms, sensor data processing, and motor control. Each programming language offers unique advantages in terms of syntax, libraries, and ease of implementation, catering to diverse preferences and requirements. Selecting the appropriate programming language based on the complexity of the robot's tasks and the programmer's proficiency is crucial in optimizing the robot's performance and responsiveness.
Circuitry Setup
The circuitry setup of line following robots encompasses the electronic components, wiring, and connections that enable seamless communication and control between the software and hardware components. An efficient circuit design that accommodates sensor inputs, motor commands, and power distribution is essential for ensuring the robot functions reliably and accurately. By organizing and securing the circuitry within the robot's architecture, potential interference, signal loss, or malfunctioning can be mitigated, enhancing the overall performance and stability of the robot's operations.
Programming Techniques for Line Following Robots
Line following robots rely heavily on precise programming techniques to navigate predefined paths with accuracy and efficiency. Understanding the intricacies of programming is crucial in ensuring the seamless operation of these intelligent machines. In this section, we will delve deep into the essential aspects of programming techniques for line following robots, examining the specific elements, benefits, and considerations that play a pivotal role in their functionality.
Basic Algorithmic Structure
Line Detection Logic
Line detection logic forms the core foundation of how line following robots interpret and respond to the signals received from the sensors. By implementing robust line detection algorithms, these robots can stay on track and make timely adjustments to maintain their course. The key characteristic of line detection logic lies in its ability to differentiate between contrasting colors or patterns, which is essential for following designated paths accurately. This approach proves to be a popular choice in developing line following robots due to its reliability and straightforward implementation. Moreover, the unique feature of line detection logic is its adaptability to varying light conditions, offering a versatile solution for different environments. Despite its effectiveness, one limitation of this method is its susceptibility to false readings in scenarios of extreme contrast or unusual patterns.
Decision-Making Process
The decision-making process in line following robots involves analyzing the data collected from sensors to determine the appropriate actions to stay on the prescribed path. This crucial aspect guides the robot's movements, ensuring optimal navigation along the designated route. An essential characteristic of the decision-making process is its real-time responsiveness, allowing the robot to make swift adjustments based on sensor inputs. This methodology is favored for its efficiency and accuracy, making it a prime choice for line following applications. The distinctive feature of the decision-making process is its adaptive nature, enabling the robot to adapt to changing conditions and maintain course integrity. However, one potential drawback is the complexity of decision algorithms, which can impact real-time processing speed and decision accuracy.
Code Optimization Strategies
Efficient Loops
Efficient loops play a significant role in optimizing the code execution of line following robots, enhancing their overall performance and responsiveness. By streamlining repetitive tasks through efficient loop structures, robots can interpret sensor data efficiently and act promptly to maintain their path. The key characteristic of efficient loops is their ability to minimize redundant operations, thereby conserving computational resources and improving response times. This approach is a popular choice for enhancing the efficiency of line following robot programs due to its effectiveness in reducing processing overhead. The unique feature of efficient loops lies in their versatility, allowing programmers to fine-tune loop iterations for different robot speeds and sensor sensitivities. While advantageous in most cases, over-optimization of loops may lead to reduced code clarity and maintainability.
Variable Management
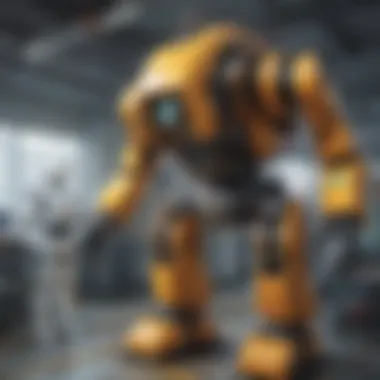
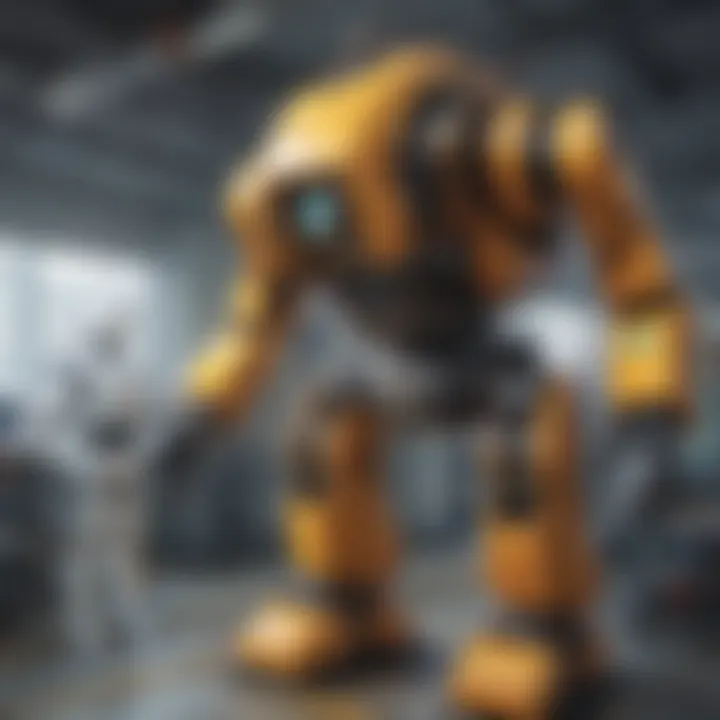
Effective variable management is essential for organizing and storing data within line following robot programs, facilitating smooth execution and reliable decision-making processes. By structuring variables efficiently, programmers can streamline data access and manipulation, optimizing overall program functionality. The key characteristic of variable management is its role in maintaining data integrity and coherence throughout the program execution cycle. This strategic approach proves to be a popular choice for enhancing program structure and readability in line following robot applications. The unique feature of variable management is its scalability, allowing for the dynamic allocation of memory resources based on the robot's operational requirements. However, improper variable handling can lead to memory leaks and runtime errors, affecting the robot's performance and stability.
Testing and Debugging Methods
Simulation Tools
Simulation tools are invaluable assets in the development and testing phase of line following robots, offering a virtual environment to validate program functionalities and behavior before actual deployment. By simulating various scenarios and sensor inputs, developers can identify potential issues and refine algorithms without risking hardware components. The key characteristic of simulation tools is their ability to provide real-time feedback on robot performance, aiding in rapid iteration and optimization of code. This feature makes simulation tools a favored choice for mitigating risks and ensuring the reliability of line following robot programs. The unique aspect of simulation tools lies in their flexibility, allowing for simulation of diverse terrain conditions and obstacle scenarios to enhance the robot's adaptive capabilities. Despite their advantages, reliance on simulation alone may overlook hardware-specific quirks and nuances, necessitating real-world validation for comprehensive testing.
Error Handling
Error handling mechanisms are vital safeguards in line following robot programs, enabling effective detection and resolution of anomalies during operation. By implementing robust error handling protocols, developers can ensure system stability and prevent critical failures that may lead to erratic behavior. The key characteristic of error handling is its capacity to anticipate and address potential issues proactively, minimizing disruption to the robot's functioning. This proactive approach is highly beneficial for maintaining the integrity of line following robot processes and mitigating adverse impacts of errors. The unique feature of error handling is its fault tolerance, empowering robots to recover gracefully from unexpected situations and resume normal operations seamlessly. However, overly complex error handling routines may introduce additional overhead, impacting the robot's responsiveness and real-time decision-making capabilities.
Advanced Applications and Future Prospects
In delving deeper into the captivating realm of line following robots, a significant emphasis lies in exploring their advanced applications and future prospects. This section sheds light on the pivotal role these intelligent robots play in shaping various industries and educational domains. By examining their adaptability and potential advancements, we gain a profound insight into the evolving landscape of robotics technology.
Industrial Automation
Warehouse Management
Warehouse management stands as a cornerstone in the application of line following robots within industrial automation. The seamless coordination of these robots within warehouse settings streamlines logistics operations, enhancing efficiency and productivity. The key characteristic of warehouse management lies in its ability to optimize storage, retrieval, and transportation processes. This approach proves to be a popular choice for industries seeking enhanced workflow automation. The unique feature of warehouse management lies in its adaptable nature, allowing for customization to specific warehouse layouts, thereby offering tailored solutions. However, challenges such as initial setup costs and integration complexities warrant careful consideration.
Assembly Lines
In the realm of assembly lines, line following robots revolutionize production processes with their precision and reliability. The key characteristic of assembly lines integration is the seamless orchestration of multiple robots to achieve synchronized assembly tasks. This integration is a beneficial choice for industries aiming to boost manufacturing speed and accuracy. The unique feature of assembly lines lies in the orchestration of robotic movements to minimize downtime and maximize throughput. However, challenges such as programming intricacies and maintenance requirements necessitate strategic planning for optimal utilization.
Educational Use Cases
STEM Education
The incorporation of line following robots in STEM education fosters hands-on learning experiences, engaging students in robotics principles and programming logic. The key characteristic of STEM education integration is its ability to cultivate critical thinking and problem-solving skills through robot experimentation. This educational approach proves to be a popular choice for schools seeking to nurture future innovators in technology. The unique feature of STEM education lies in its interdisciplinary approach, bridging science, technology, engineering, and math concepts seamlessly. While advantageous in skill development, challenges such as resource availability and training requirements need to be addressed.
Robotics Competitions
Robotics competitions serve as platforms for students to showcase their creativity and technical prowess through the design and programming of line following robots. The key characteristic of robotics competitions is the focus on collaboration, innovation, and competitive spirit among participants. This avenue is a beneficial choice for nurturing teamwork and problem-solving competencies in a competitive setting. The unique feature of robotics competitions lies in the real-world application of robotics knowledge through competitive challenges, inspiring continuous learning. However, challenges such as time constraints and resource management add complexity to the competition dynamics.
Innovations and Technological Advances
AI Integration
The integration of artificial intelligence (AI) enhances the capabilities of line following robots by enabling adaptive decision-making and learning. The key characteristic of AI integration lies in its ability to analyze sensor data and refine navigation strategies in dynamic environments. This strategic integration is a beneficial choice for enhancing robot autonomy and performance in complex scenarios. The unique feature of AI integration lies in the iterative learning process, allowing robots to adapt to changing conditions autonomously. However, challenges such as data privacy concerns and ethical implications of AI decision-making underscore the importance of responsible AI deployment.
Machine Learning in Robotics
The infusion of machine learning in robotics empowers line following robots with predictive capabilities and continual optimization. The key characteristic of machine learning in robotics is its utilization of algorithms to analyze data and improve robotic decision-making over time. This integration proves beneficial for enhancing robot precision and adaptability to diverse operating conditions. The unique feature of machine learning in robotics lies in the self-learning algorithms that enable robots to refine their behavior based on previous experiences. Challenges such as data complexity and model interpretability warrant a nuanced approach to harnessing the full potential of machine learning in robotics.