Mastering the Art of Printing Designs on Fabric: A Complete Guide for Creatives
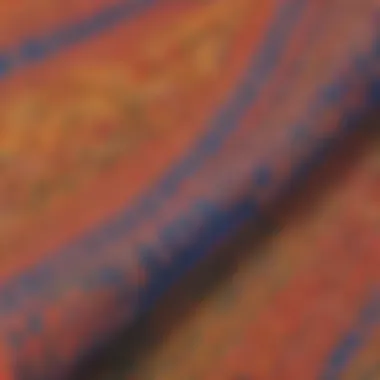
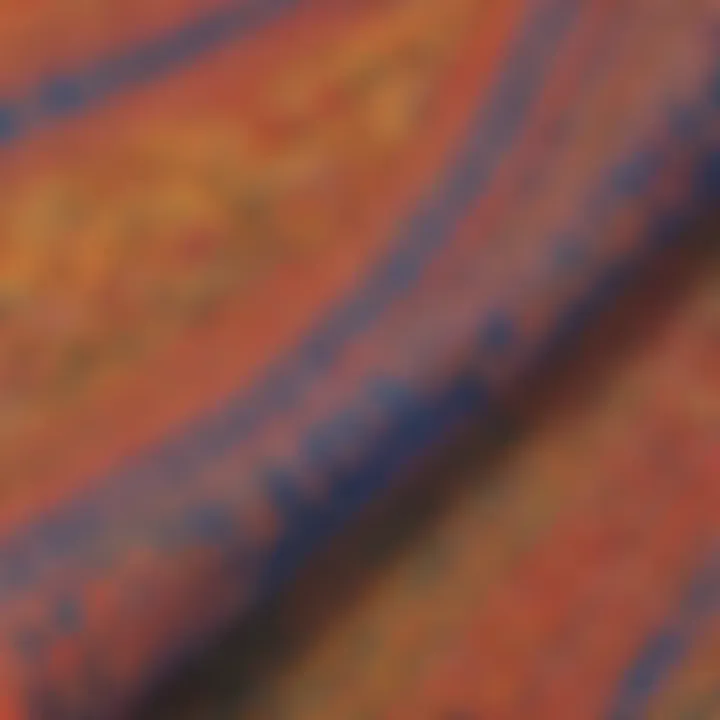
Science Fun Facts
Understanding the nuances of fabric printing entails delving into an amalgamation of artistry and precision. While many may view it as a straightforward process, the intricate details can captivate both beginners and experts alike. The interplay of colors, textures, and techniques culminates in breathtaking designs that adorn fabrics in mesmerizing ways.
Discover the Wonders of Science
Exploring the realm of fabric printing unveils a rich tapestry of scientific concepts intertwined with artistic expression. From the chemical interactions between dyes and fibers to the engineering precision required for screen printing, every facet merges creativity with methodology. Educational videos and interactive tools serve as gateways to understanding the real-life applications of different printing techniques.
Science Quiz Time
Engage in a mental odyssey through interactive quizzes that unravel the complexities of fabric printing. From multiple-choice questions testing your knowledge of color theory to brain teasers challenging your understanding of textile chemistry, each puzzle offers a peek into the meticulous world of fabric design. Learning through gamification transforms the learning process into a thrilling adventure of discovery.
Science Experiment Showcase
Embark on a journey of tactile exploration with fun and engaging fabric printing experiments. Follow step-by-step instructions to create your own eco-friendly dyes or explore the art of block printing with readily available materials. Safety tips and precautions ensure a seamless and secure experience, fostering creativity balanced with responsibility.
Introduction
In the realm of creative expression, fabric printing stands as a captivating intersection between artistry, technology, and personal style. This comprehensive guide endeavors to unravel the intricate process of imprinting designs onto fabric, sparking imagination and ingenuity among enthusiasts and novices alike. Embarking on this journey not only unveils the essence of creative exploration but also grants the power to transform ordinary fabric into a personalized masterpiece.
Fabric printing serves as a gateway to a realm where colors dance harmoniously, where patterns narrate stories, and where individuality finds its voice amidst threads and fibers. Understanding the nuances of fabric printing elevates the appreciation for design intricacies, color theories, and textile characteristics. It is a fusion of technical precision and artistic liberty, laying the foundation for boundless creativity to flourish.
Delving deeper, this guide illuminates the diverse array of fabric printing techniques at one's disposal - from the timeless artistry of screen printing to the precision of digital printing, the heritage-rich craft of block printing, and the innovation of transfer printing. Each technique bestows its unique charm and challenges, inviting designers to explore and expand their horizons in the realm of textile artistry.
Moreover, before the first drop of ink touches the fabric, considerations loom large on the horizon. Factors such as fabric type and fiber content play a pivotal role in determining optimal printing methods, ensuring longevity and vibrancy in the final output. Design complexity intricacies dictate the choice between techniques, while color options set the mood and tone for the entire design endeavor. These pre-printing considerations serve as the compass guiding creators towards a successful and gratifying fabric printing journey.
The journey towards fabric printing mastery begins with a single step - a step that holds the promise of untold creativity, boundless expression, and tangible artistry. Let us traverse this path together, unraveling the secrets, techniques, and insights that pave the way to crafting exquisite fabric designs that resonate with individuality and craftsmanship.
Understanding Fabric Printing
Understanding Fabric Printing is a crucial aspect when delving into the art of printing designs on fabric. It serves as the foundation for creating high-quality, visually appealing fabric prints. By comprehending the different fabric printing techniques available and factors to consider before printing, individuals can make informed decisions that align with their design goals. This section aims to explore the significance of Understanding Fabric Printing, emphasizing the nuances of each printing technique and how they influence the final outcome. Readers will gain insight into the technical aspects of fabric printing, enabling them to navigate the process with confidence and precision.
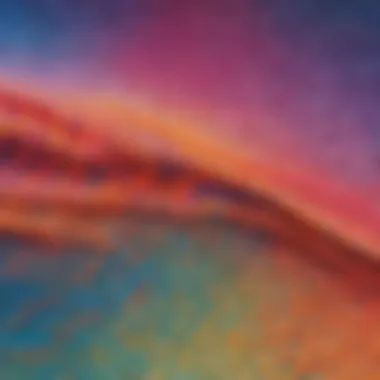
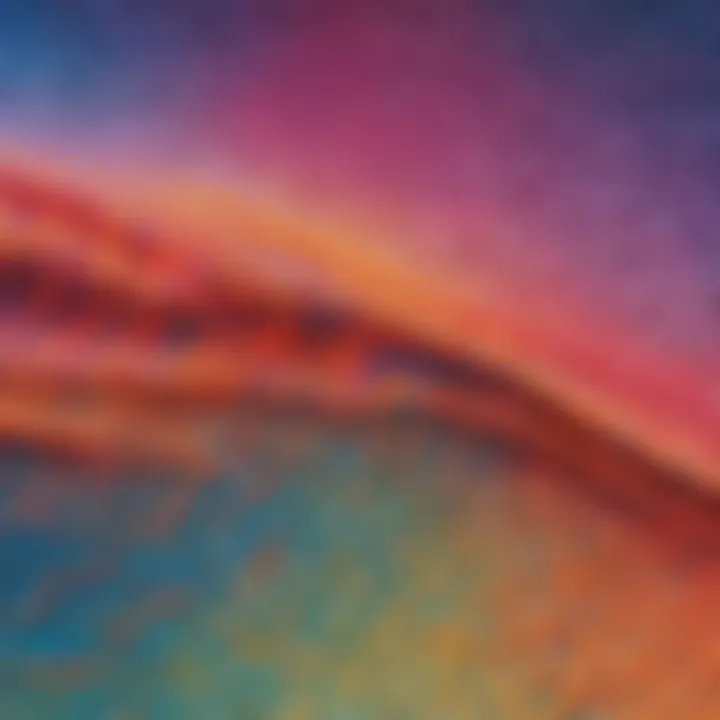
Types of Fabric Printing Techniques
Screen Printing
Screen Printing stands out as a traditional yet effective method in the realm of fabric printing. Its meticulous process involves transferring designs onto fabric through a mesh screen, resulting in precise and vibrant prints. The key characteristic of Screen Printing lies in its versatility, allowing for intricate designs and a wide range of color options. While Screen Printing demands expertise and attention to detail, its ability to create durable prints makes it a favored choice for fabric artists seeking long-lasting results. Despite its time-consuming nature, Screen Printing delivers excellent clarity and consistency, enhancing the visual appeal of printed fabric.
Digital Printing
Digital Printing represents a modern approach to fabric printing, harnessing technology to produce intricate designs with unmatched accuracy. By directly applying designs onto fabric using advanced printers, Digital Printing offers quick turnaround times and eliminates the need for complex setups. The key characteristic of Digital Printing is its ability to reproduce intricate details and gradients seamlessly, catering to designs with a high level of complexity. While Digital Printing excels in producing vivid colors and photorealistic prints, it may present limitations in color matching and fabric compatibility.
Block Printing
Block Printing embodies a traditional craft where designs are carved onto blocks, which are then used to stamp designs onto fabric. The key characteristic of Block Printing lies in its artisanal appeal and handcrafted aesthetic. This technique allows for personalized touches and unique variations in each print, adding a bespoke quality to fabric designs. While Block Printing offers creativity and artistic freedom, it can be labor-intensive and may require expertise in block carving to achieve intricate designs.
Transfer Printing
Transfer Printing involves creating designs on transfer paper and then transferring them onto fabric using heat or pressure. The key characteristic of Transfer Printing is its ability to achieve intricate designs with minimal setup, making it an efficient choice for small-scale production or custom prints. By offering versatility in design placement and color vibrancy, Transfer Printing enables artists to explore creative possibilities with ease. While Transfer Printing streamlines the printing process, it may present challenges in achieving color consistency and durability over time.
Factors to Consider Before Printing
Before embarking on the fabric printing journey, several factors merit consideration to ensure successful outcomes. Exploring fabric type and fiber content is crucial, as different materials react uniquely to printing techniques and colorants. Design complexity plays a significant role in determining the feasibility of chosen printing methods, with intricate designs requiring precision and compatible printing processes. Additionally, understanding color options and their interaction with fabrics is essential for achieving desired color outcomes. By delving into these considerations, individuals can make informed decisions that optimize the fabric printing process and elevate the quality of printed designs.
Preparing for Fabric Pieintng
The process of preparing for fabric painting is a critical step in ensuring the quality and longevity of the final design. Before diving into the artistic aspect of fabric printing, it is essential to lay a solid foundation by choosing the right design and priming the fabric for optimal ink absorption.
Choosing a Design
When it comes to selecting a design for fabric printing, there are two primary avenues to consider: creating your own design or opting for a pre-made design. Both options offer distinct advantages depending on your artistic vision and technical proficiency.
Creating Your Own Design

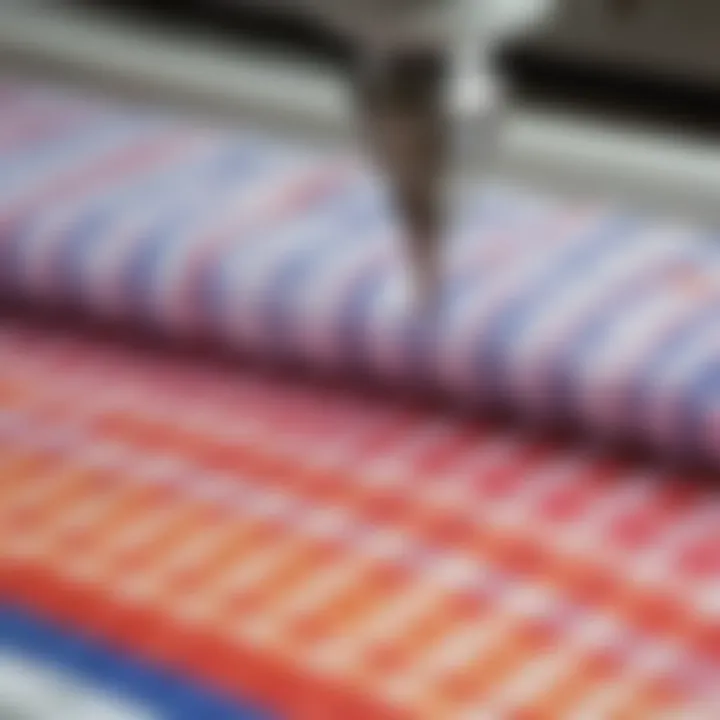
Creating your own design provides a unique opportunity for self-expression and originality in your fabric prints. By handcrafting a design from scratch, you can tailor every element to suit your preferences, ensuring a truly custom piece of art. This hands-on approach allows for complete creative control and the freedom to experiment with varying styles and motifs.
On the flip side, creating your own design demands artistic skill and a keen eye for detail. It requires ample time and dedication to conceptualize, draft, and refine your design before transferring it onto fabric. While the process may be labor-intensive, the end result is a one-of-a-kind creation that reflects your personal taste and style.
Selecting a Pre-made Design
Alternatively, selecting a pre-made design can offer a convenient and time-efficient solution for fabric printing projects. Pre-made designs are predesigned patterns or motifs that you can readily purchase or download for immediate use. This option is ideal for those seeking quick turnaround times or lacking the expertise in graphic design.
Opting for a pre-made design eliminates the need for extensive design work, making it a suitable choice for beginners or individuals with time constraints. With a plethora of design options available online or in stores, you can easily find a design that aligns with your aesthetic preferences and project requirements.
Pre-treating the Fabric
Pre-treating the fabric is a crucial preparatory step that ensures optimal ink penetration and color vibrancy in the final print. This process involves washing and drying the fabric to remove any impurities or sizing agents that may hinder the adhesion of the ink.
Washing and Drying
Washing the fabric helps eliminate excess dyes, chemicals, or starches that could affect the printing quality. By launderigii the fabric, you create a clean canvas for the design while also pre-shrinking the material to prevent distortion post-printing. Drying the fabric thoroughly is equally important to avoid any residual moisture that could impact ink adhesion during the printing process.
l Ironing
Ironing the fabric post-washing and drying helps smoothen out any wrinkles or creases that might interfere with the printing process. A well-ironed fabric provides a flat and even surface for seamless design transfer and print clarity. Additionally, ironing helps ensure that the fabric is in the ideal condition for accepting the ink evenly across the surface, resulting in a professional-looking fabric print.
Printing the Design
In this pivotal section of the article, we delve into the crux of fabric printing - Printing the Design. This segment forms the core of the entire fabric printing process, playing a fundamental role in bringing a design to life on the chosen fabric. Understanding the intricacies of Printing the Design is crucial for achieving the desired outcome. Details about ink types, coverage, and design intricacies are paramount to the success of this stage. Ensuring proper alignment and color intensity are just some of the key elements to observe during the Printing the Design phase.
Step-by-Step Printing Process
Preparing the Printing Area
Discussing Preparing the Printing Area is essential as it sets the foundation for a successful printing process. This step involves prepping the work surface, ensuring it is clean, flat, and well-equipped with all necessary tools. The efficiency and accuracy of the printing outcome heavily rely on the meticulous preparation of the printing area. Paying attention to details such as lighting and space utilization greatly contribute to the overall quality and precision of the output. Factoring in ergonomic considerations can make the Printing Area not just functional but also ergonomically friendly for the individual executing the printing task. Preparing the Printing Area can significantly impact the workflow and efficiency of the printing process. Having a well-organized and clutter-free space facilitates a smooth transition between printing stages and minimizes errors due to distractions or disorganization.
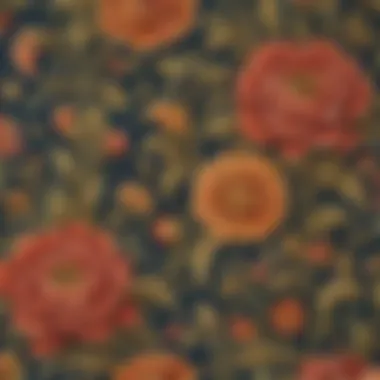
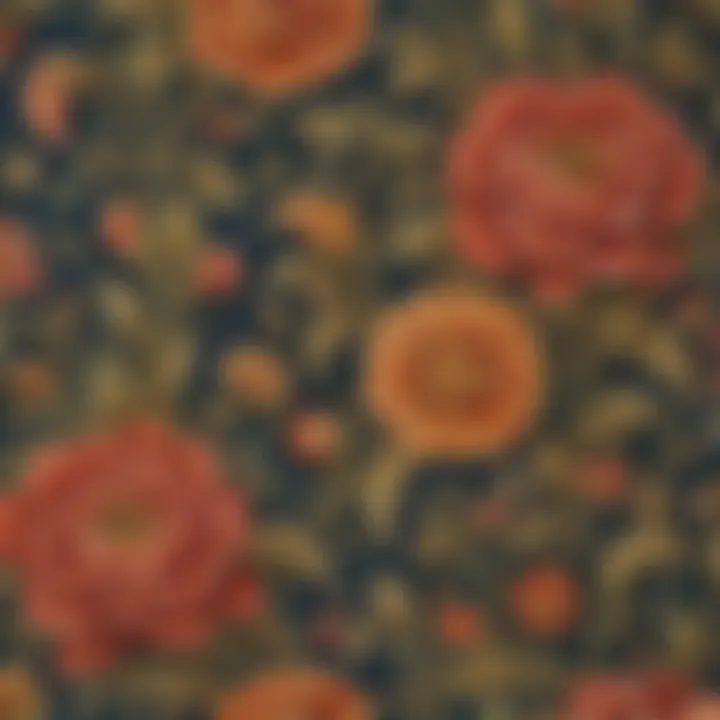
Setting Up the Equipment
The process of Setting Up the Equipment plays a vital role in ensuring a seamless printing experience. Having the necessary printing tools and machinery ready and appropriately configured is key to achieving consistent results. The precision and calibration of the equipment are paramount to the accurate reproduction of the design onto the fabric. Addressing equipment maintenance and calibration enhances the longevity and accuracy of the printing process. Familiarizing oneself with the equipment settings and functionalities is crucial for smooth operation and troubleshooting potential issues that may arise during printing.
Printing the Design
The act of Printing the Design is where the magic truly happens, as the envisioned design starts taking form on the fabric. Attention to detail during the printing process is critical for capturing the nuances and intricacies of the design accurately. The choice of printing method and technique significantly impacts the final outcome of the printed design. Factors such as ink consistency, pressure, and speed play a critical role in achieving a high-quality print. Adhering to precise printing guidelines ensures the design is faithfully replicated on the fabric, capturing all its subtleties and intricacies.
Curing or Setting the Print
Post-printing, the step of Curing or Setting the Print serves to seal and enhance the durability of the printed design. Proper curing or setting procedures help the ink bond securely with the fabric fibers, ensuring longevity and colorfastness of the print. Understanding the optimal curing techniques based on the ink type and fabric material is crucial for maintaining the integrity of the design over time. Careful consideration of curing temperatures, duration, and post-curing treatments can significantly impact the final look and feel of the printed fabric.
Troubleshooting Common Printing Issues
Blurred Images
Addressing Blurred Images is pivotal in maintaining the sharpness and clarity of the printed design. Fuzzy or obscure images can detract from the overall quality of the print, necessitating thorough troubleshooting to identify and rectify the underlying causes. Factors such as improper image resolution, screen alignment, or ink viscosity can contribute to blurred images during printing. Implementing precise printing protocols and regular maintenance can help mitigate the occurrence of blurred images and maintain print quality.
Inconsistent Colors
Consistency in color reproduction is vital for achieving uniformity and accuracy in the printed design. Inconsistent Colors can result from variables such as ink mixing ratios, color profiles, or printing settings. Calibrating equipment, conducting color tests, and monitoring environmental conditions can help minimize color discrepancies during printing. Establishing a standardized color management process can aid in achieving color fidelity and consistency across multiple print runs.
Ink Bleeding
The phenomenon of Ink Bleeding can pose challenges to the quality and precision of the printed design. Ink bleeding occurs when ink spreads uncontrollably on the fabric, causing smudges and distortions in the design. Understanding the root causes of ink bleeding, such as improper ink penetration or excessive pressure during printing, is paramount to implementing preventive measures. Adjusting ink viscosity, optimizing pressure settings, and conducting regular equipment maintenance can help mitigate ink bleeding issues and uphold the integrity of the printed design.
This comprehensive guide aims to equip individuals with the knowledge and insights necessary to navigate the intricate process of fabric printing successfully. From meticulous pre-printing preparations to troubleshooting common printing issues, each stage is meticulously detailed to empower readers with the expertise needed to excel in fabric printing endeavors.
Finishing Touches and Care
In the realm of fabric printing, Finishing Touches and Care play a pivotal role in ensuring the longevity and quality of your printed designs. Once the printing process is complete, taking the necessary steps to fix and maintain the print becomes crucial. Finishing Touches and Care encompasses post-printing tasks that enhance the durability and vibrancy of the print, ensuring it withstands wear and washing.
When it comes to Fixing the Print, Heat Setting emerges as a critical step in the process. Heat Setting involves applying heat to the printed fabric using an iron or heat press to cure the ink, making it wash-proof and colorfast. This process helps the design adhere firmly to the fabric, preventing fading and ensuring a long-lasting print. Failure to properly Heat Set the print may result in the ink washing off or bleeding during laundering.
Washing Instructions follow Heat Setting and are equally important in maintaining the integrity of the print. Providing suitable guidance on washing and caring for the printed fabric ensures that the design retains its brightness and sharpness over time. By employing the correct washing methods, such as using gentle detergents, washing at the proper temperature, and avoiding harsh washing techniques, you can extend the life of the print. Incorrect washing practices can lead to premature fading, distortion of the design, or even peeling of the print.
Conclusion
Importance of wirk.d