Crafting a Highly Functional Robot: An In-Depth Exploration
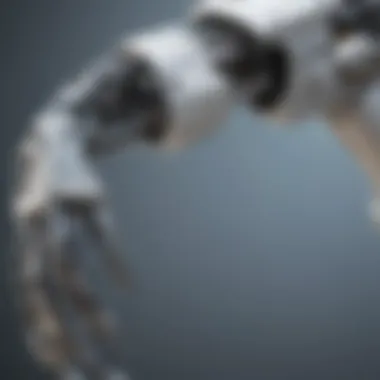
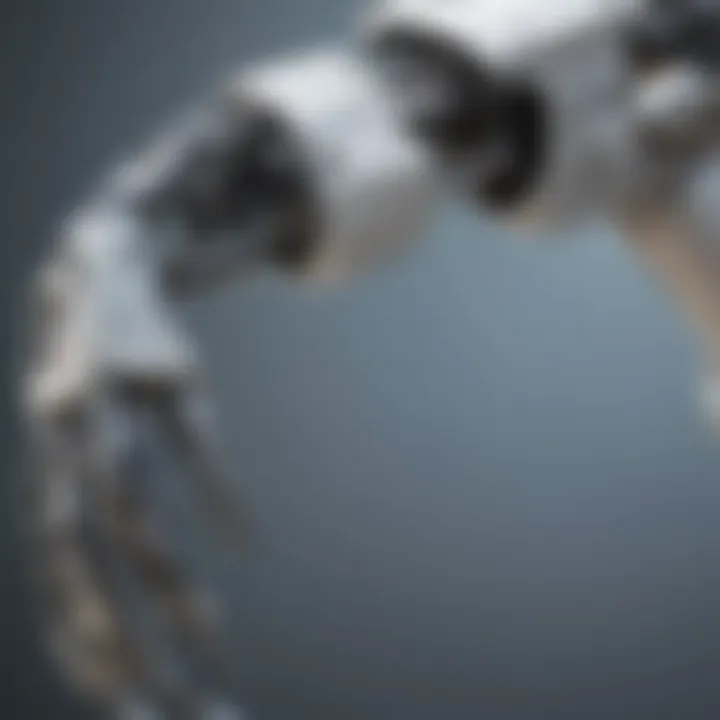
Science Fun Facts
As we delve into the world of creating functional robots, it's fascinating to uncover some quirky science stories and delve into amazing scientific records related to robotics. Did you know that the largest robot ever built stands over 200 feet tall and weighs a whopping 1,400 tons? This colossal machine is a true marvel of engineering, showcasing the incredible capabilities of robotic technology.
Exploring Robotics Concepts
In our exploration of creating a functional robot, let's dig into the core scientific concepts that govern the field. From understanding how sensors detect the environment to the intricacies of programming robots to perform specific tasks, there is a world of knowledge waiting to be unravelled. Educational videos and animations can provide a visual insight into these complex concepts, making learning both interactive and engaging.
Engineering a Robot
Building a robot involves a series of carefully planned steps that culminate in the assembly of a fully operational machine. From selecting the right materials to programming the robot's movements, every aspect requires precision and attention to detail. By following step-by-step instructions and being mindful of safety tips and precautions, aspiring robot engineers can bring their creations to life with confidence.
Robotics in Action
The real-life applications of robotics are vast and diverse, ranging from autonomous drones used for various tasks to sophisticated robotic arms employed in manufacturing processes. By witnessing robots in action, whether in industrial settings or daily life, we gain a deeper appreciation for the impact of technology on modern society. Through hands-on experiences and interactive learning tools, the potential of robotics becomes not just a concept but a tangible reality.
Introduction
Understanding the Basics
Importance of Research
Research serves as the cornerstone of any successful project, and in the realm of creating a functional robot, its significance cannot be overstated. Delving into the depths of research allows designers and engineers to gather essential information, analyze existing technologies, and adapt innovative solutions to their design challenges. The meticulous nature of research ensures that each component and functionality of the robot is based on informed decisions, leading to a more efficient and effective end product. However, research demands time and resources, posing a challenge in the fast-paced world of robotics.
Identifying the Purpose
Identifying the purpose of the robot is a crucial first step in the design process. This aspect sets the foundation for all subsequent decisions, guiding the direction of the project and defining its overarching goal. By clearly defining the purpose, designers can align their efforts towards achieving specific functionalities and performance benchmarks, ensuring that the end result fulfills its intended role effectively. However, a narrow or overly broad purpose can limit the robot's adaptability and utility in different scenarios, making the identification process a delicate balance of specificity and flexibility.
Choosing the Right Components
Selecting the appropriate components is akin to choosing the building blocks of the robot. Each component contributes to the overall functionality and performance, making the selection process a critical aspect of the design phase. From motors to sensors, the choice of components determines the capabilities and limitations of the robot. Opting for high-quality components enhances the reliability and durability of the robot, ensuring smoother operations and longevity. However, the vast array of options in the market poses a challenge, requiring designers to conduct thorough research and testing to identify the optimal components for their specific design needs.
Setting Clear Objectives
Defining Functionality Goals
Defining functionality goals outlines the specific tasks and operations that the robot must accomplish. This step (continue in similar manner)
Design Phase
In the realm of creating a functional robot, the Design Phase stands as a pivotal juncture where ideas transform into tangible blueprints governing the robot's construction. This section delves into the critical aspect of design - a foundational element ensuring the robot's efficacy and functionality. The significance of the Design Phase resonates in its ability to lay the groundwork for subsequent stages of the robot-building process. Analyzing the importance of this phase sheds light on its role in streamlining the construction process, minimizing errors, and maximizing efficiency.
Creating a Blueprint
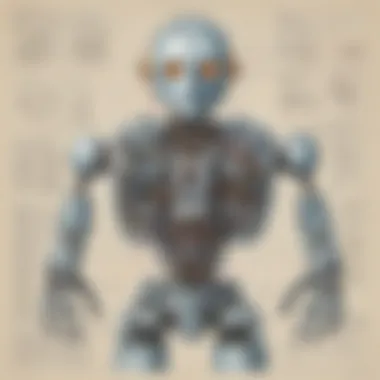
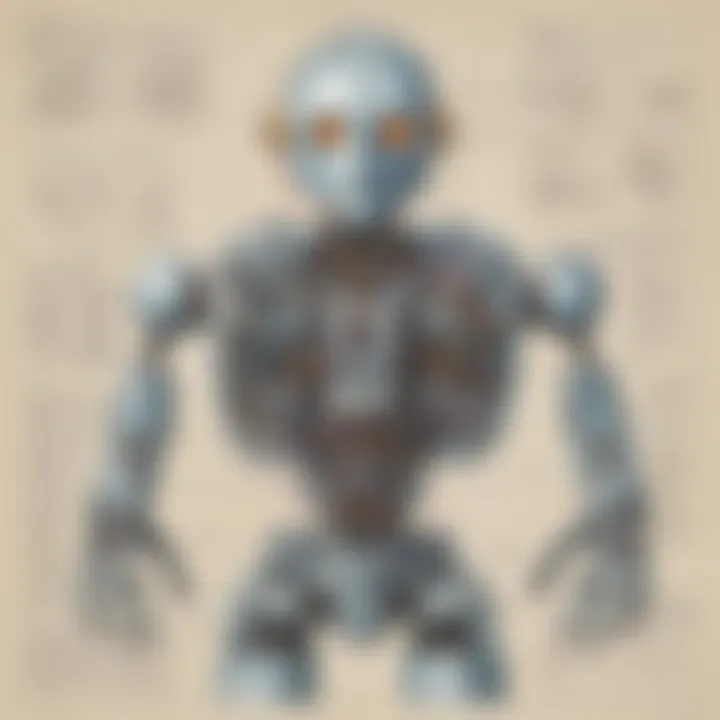
Sketching Initial Designs
Delving into the realm of Sketching Initial Designs brings to the forefront the essence of visualizing concepts in their raw form. Sketching serves as the primary means to translate abstract ideas into concrete visual representations, facilitating communication and clarity throughout the design phase. The key characteristic of Sketching Initial Designs lies in its ability to unleash creativity and innovative thinking, allowing designers to explore various concepts before committing to a final design. Despite its simplicity, sketching embodies a potent tool for brainstorming and refining ideas, propelling the design process forward with a sense of fluidity and adaptability.
Incorporating Feedback
Incorporating Feedback embodies a crucial step in refining initial designs by integrating external perspectives and insights. This process fosters collaboration and ensures that multiple viewpoints converge to enhance the overall design. The essence of this aspect lies in its ability to iterate on existing concepts, enabling continual improvement and refinement based on valuable feedback. Embracing feedback cultivates a culture of openness to diverse opinions, enriching the design process with a multiplicity of ideas and considerations while nurturing a sense of collective ownership and commitment.
Finalizing Schematics
As the final piece of the blueprint puzzle, Finalizing Schematics encapsulates the conclusive stage of design refinement, where detailed plans and specifications solidify. The key characteristic of this phase is the meticulous attention to detail and precision in articulating each component's placement and function. Finalizing Schematics serves as the blueprint's polished version, ready for implementation during the construction phase, highlighting the intricate interplay of mechanical and electrical elements. While the advantages of final schematics lie in their clarity and specificity, potential disadvantages may arise from overcommitting to predetermined designs, limiting flexibility in the face of unforeseen challenges.
Prototyping
Embarking on the Prototyping phase unveils a transformative stage where designs transition from theoretical constructs to physical prototypes, embodying the manifestation of creative vision. Each subsection within Prototyping plays a distinctive role in refining and validating the design, paving the way for functional implementation and fine-tuning.
Assembling Prototype Parts
The intricate process of Assembling Prototype Parts marks a fundamental stage where individual components meld into a cohesive structure, mirroring the envisioned design. The distinctive allure of assembling lies in its hands-on approach to materializing abstract concepts into tangible forms, enabling designers to witness the gradual transformation of ideas into reality. While advantageous for its tactile engagement and visual representation, challenges may arise in aligning components precisely and troubleshooting assembly intricacies.
Testing Functionality
Testing Functionality emerges as a critical phase aimed at evaluating the operational capabilities of the prototype, ensuring that each component functions harmoniously within the robotic framework. The defining characteristic of this stage is its empirical approach to verifying the design's practical feasibility, identifying potential flaws or inefficiencies that necessitate refinement. Testing functionality serves as a litmus test for the prototype's efficacy and performance, setting the stage for iterative improvements based on real-world testing and observation.
Refining Design
Refining Design encapsulates the iterative process of enhancing the prototype's aesthetics, performance, and functionality based on testing outcomes and user feedback. The essence of refinement lies in its adaptive nature, allowing designers to implement targeted modifications that optimize the robot's overall efficiency. While refining design fosters continual improvement and innovation, challenges may arise in balancing the quest for perfection with pragmatic constraints, requiring thoughtful decision-making and prioritization of design objectives.
Software Integration
Navigating the realm of Software Integration brings into focus the critical juncture where coding, testing, and compatibility converge to breathe life into the robotic system. Each aspect within Software Integration plays a distinct role in ensuring that the robot's software complements its hardware counterparts seamlessly.
Coding Algorithms
Coding Algorithms form the foundational language through which the robot's behavior and functions are orchestrated, setting the logic and algorithms governing its interactions with the environment. The inherent characteristic of coding algorithms lies in its structured approach to defining computational rules and processes, empowering the robot to execute tasks with precision and efficiency. Integrating coded algorithms into the robot's framework enhances its autonomy and responsiveness, opening avenues for complex behavior and adaptive functionalities.
Testing Programming
Testing Programming acts as a quality assurance checkpoint, validating the integrity and functionality of the coded algorithms within the robot's software framework. The crucial aspect of testing programming resides in its role as a diagnostic tool, identifying bugs, errors, and discrepancies that may hinder the robot's performance. Through systematic testing, programmers can pinpoint inefficiencies and fine-tune the codebase, ensuring seamless integration and optimal functionality within the robotic system.
Ensuring Compatibility
Ensuring Compatibility stands as a cornerstone in the software integration process, emphasizing the need for cohesive alignment between various software components and hardware configurations. The primary characteristic of compatibility lies in its capacity to foster interoperability and synergy among disparate software modules, ensuring that the overall software architecture functions harmoniously. By addressing compatibility challenges early on, designers can preempt integration hurdles and streamline the software deployment process, enhancing the robot's operational efficiency and reliability.
Construction Process
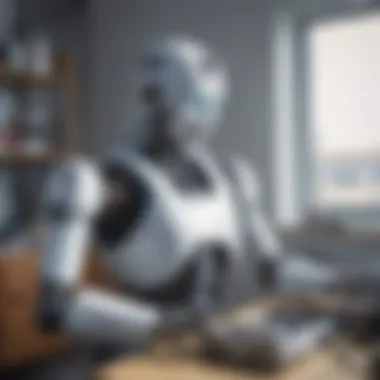
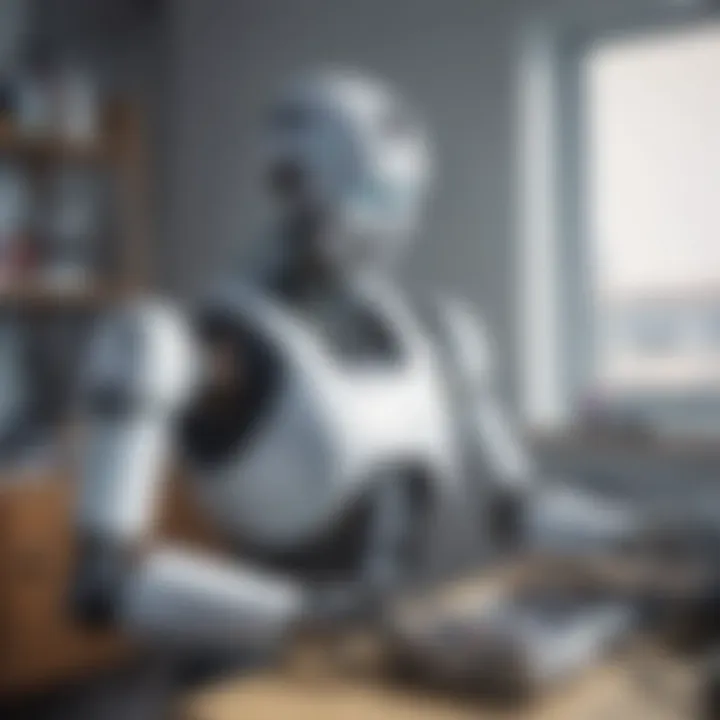
The Construction Process plays a pivotal role in the overall scheme of designing and building a functional robot. It encompasses a series of crucial tasks that involve bringing together various components to form the physical structure of the robot. This phase is where the abstract ideas and design concepts transition into tangible reality, requiring meticulous attention to detail and precision to ensure the robot's functionality and efficiency. Proper execution of the Construction Process is fundamental in determining the success of the entire project.
Mechanical Assembly
Joining Structural Components
The aspect of Joining Structural Components is a fundamental step in the Mechanical Assembly phase of constructing a robot. It involves securely connecting the different parts of the robot's body to create a sturdy and stable framework. The key characteristic of Joining Structural Components lies in its ability to provide structural integrity and support to the robot, ensuring that it can withstand physical stresses and movements during operation. This method is a popular choice for this article due to its simplicity, cost-effectiveness, and reliability. The unique feature of Joining Structural Components is its versatility in accommodating various shapes and sizes of components, offering flexibility in design. While it offers ease of construction and assembly, the potential disadvantages include reduced load-bearing capacity in complex structures.
Securing Moving Parts
Securing Moving Parts is another critical aspect of Mechanical Assembly that focuses on ensuring proper attachment and functionality of components that facilitate motion within the robot. The key characteristic of Securing Moving Parts is its role in preventing dislodgement or misalignment of crucial elements, thereby enhancing the robot's operational precision and safety. This method is considered beneficial for this article due to its emphasis on smooth, controlled movement and reduced wear and tear. The unique feature of Securing Moving Parts is its ability to maintain operational efficiency even under varying environmental conditions, making it ideal for diverse applications. While it improves the overall performance of the robot, challenges may arise concerning intricacies in alignment and maintenance requirements.
Calibrating Mechanics
Calibrating Mechanics is an essential aspect of Mechanical Assembly that involves fine-tuning and adjusting mechanical components to ensure optimal performance and coherence within the robot. The key characteristic of Calibrating Mechanics is its emphasis on achieving precision and accuracy in the movement and coordination of robotic parts, enhancing overall functionality. This process is favored for this article due to its capability to enhance efficiency, reduce energy consumption, and prolong the lifespan of mechanical components. The unique feature of Calibrating Mechanics lies in its ability to cater to specific design requirements, allowing for customized and optimized robotic movements. While it improves the robot's performance, challenges may arise in achieving consistent calibration across all components and systems.
Electrical Wiring
Connecting Circuitry
Connecting Circuitry is a critical aspect of the Electrical Wiring phase, focusing on establishing electrical connections between various components to enable communication and control within the robot. The key characteristic of Connecting Circuitry is its role in creating a seamless network that facilitates data transmission and power distribution, essential for the robot's operation. This method is preferred for this article due to its efficiency, compactness, and reliability in transmitting signals and power across the robotic system. The unique feature of Connecting Circuitry is its adaptability to diverse configurations, enabling the integration of complex electronic systems within the robot. While it enhances the robot's functionality, challenges may arise in managing connectivity issues and ensuring compatibility across different components.
Testing Power Sources
Testing Power Sources is a crucial aspect of Electrical Wiring that involves evaluating the performance and reliability of the power supply units used to energize the robot. The key characteristic of Testing Power Sources lies in its ability to verify the suitability and efficiency of various power sources in meeting the energy demands of the robot under different operating conditions. This process is beneficial for this article as it ensures sustained power delivery, prevents potential failures, and enhances overall safety during robot operation. The unique feature of Testing Power Sources is its capacity to detect and rectify voltage irregularities, ensuring stable and consistent power flow throughout the robotic system. While it optimizes the robot's power efficiency, challenges may arise in conducting exhaustive testing procedures and interpreting complex power data.
Implementing Safety Measures
Implementing Safety Measures is a critical aspect of Electrical Wiring that focuses on integrating protective mechanisms and protocols to safeguard the robot's operation and surrounding environment. The key characteristic of Implementing Safety Measures is its emphasis on preemptive actions to prevent accidents, mitigate risks, and ensure compliance with safety standards. This approach is necessary for this article as it prioritizes the well-being of users, the robot itself, and the workspace where it operates. The unique feature of Implementing Safety Measures is its capability to customize safety features based on specific applications and potential hazards, ensuring comprehensive protection. While it enhances the overall safety of the robot, challenges may arise in balancing safety measures with operational efficiency and avoiding over-engineering for minimal risks.
Testing and Optimization
In the realm of creating a functional robot, the phase of Testing and Optimization stands as a pivotal juncture that can make or break the efficacy of the end product. This section delves deep into the importance and nuances of Testing and Optimization in the intricate process of crafting a robot that not only functions effectively but does so with precision and reliability.
Functionality Tests
Testing Movement
Testing Movement is a critical aspect within the broader spectrum of Functionality Tests. It plays a foundational role in ascertaining the physical capabilities and limitations of the robot. The key characteristic of Testing Movement lies in its ability to assess the robot's locomotion, agility, and spatial awareness in diverse environments. This strategic evaluation is immensely beneficial for refining the robot's motion algorithms and ensuring seamless performance. Despite its significance, Testing Movement does come with its own set of challenges. The unique feature of Testing Movement is its hands-on approach to analyzing how effectively the robot maneuvers and navigates, offering real-world insights for optimization.
Ensuring Sensor Acraucy
Ensuring Sensor Accuracy holds paramount importance in maximizing the robot's functionality and responsiveness. This aspect focuses on calibrating and validating the accuracy of sensors embedded within the robot to perceive and react to its surroundings accurately. The key characteristic of Ensuring Sensor Accuracy is its meticulous attention to detail in eliminating discrepancies that may arise from sensor malfunctions or inaccuracies. By fine-tuning the sensors, the robot can make informed decisions based on reliable data, enhancing its overall performance. While Ensuring Sensor Accuracy is crucial, it requires ongoing calibration and monitoring, which can be resource-intensive. However, the unique feature of Ensuring Sensor Accuracy lies in its ability to elevate the robot's operational precision through constant vigilance and calibration.
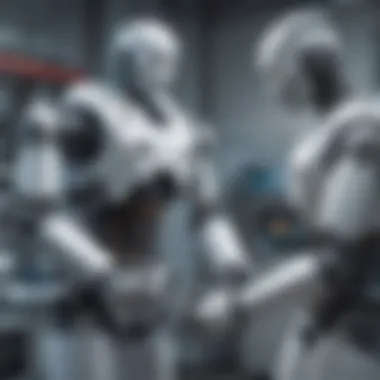
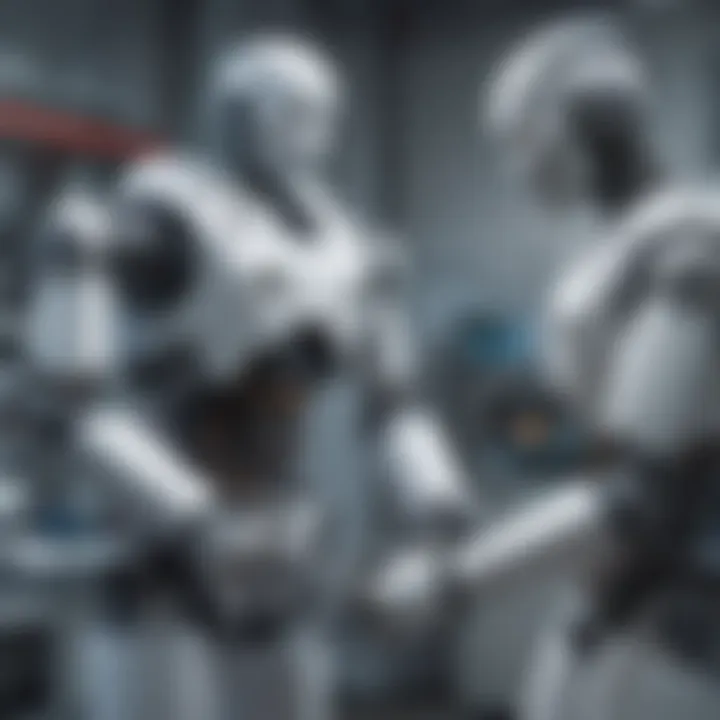
Fine-Tuning Performance
Fine-Tuning Performance acts as the refinement stage where optimizations are made to enhance the robot's overall operational efficiency. The key characteristic of Fine-Tuning Performance is its focus on streamlining the robot's actions and responses to achieve optimal functionality. This meticulous process involves adjusting parameters, refining algorithms, and eliminating bottlenecks to elevate the robot's performance to its peak. While Fine-Tuning Performance leads to significant improvements, it demands thorough testing and analysis, consuming additional time and resources. The unique feature of Fine-Tuning Performance lies in its ability to push the boundaries of the robot's capabilities by fine-tuning every aspect for improved efficiency and efficacy.
Optimizing Efficiency
Optimizing Efficiency is a critical aspect in ensuring that the robot operates at its maximum potential while conserving resources and delivering optimal performance. This section explores three key elements that contribute to the efficiency of the robot: Enhancing Speed, Minimizing Errors, and Improving Battery Life.
Enhncing Speed
Enhancing Speed plays a crucial role in boosting the robot's agility and responsiveness. The key characteristic of Enhancing Speed is its focus on accelerating the robot's movements without compromising precision. This enhancement is beneficial in scenarios where swift reactions are essential for the robot's performance, especially in dynamic environments. The unique feature of Enhancing Speed lies in its capacity to advance the robot's operational speed while maintaining control and accuracy. However, achieving higher speeds may lead to increased energy consumption and potential stability challenges.
Minimizing Errors
Minimizing Errors is a fundamental aspect of refining the robot's functionality and ensuring consistent performance. This component emphasizes the reduction of mistakes and inaccuracies in the robot's computations and actions. The key characteristic of Minimizing Errors lies in its meticulous approach to error detection, correction, and prevention through comprehensive testing and validation processes. By minimizing errors, the robot can execute tasks with precision and reliability, enhancing its overall effectiveness. Despite its benefits, the constant vigilance required for Minimizing Errors can add complexity to the development process. The unique feature of Minimizing Errors is its continual improvement cycle, where each error detected leads to refinements that bolster the robot's efficiency and accuracy.
Improvign Battery Life
Improving Battery Life is essential for sustaining the robot's operations over extended periods and minimizing downtime. This element focuses on optimizing power consumption and management to prolong the robot's battery lifespan. The key characteristic of Improving Battery Life is its strategic approach to balancing performance needs with energy efficiency, ensuring prolonged usage without frequent recharging. By enhancing battery life, the robot can operate autonomously for longer durations, increasing its productivity and usability. However, optimizing battery life may entail trade-offs in terms of performance capabilities or additional weight from larger batteries. The unique feature of Improving Battery Life lies in its ability to extend the robot's operational autonomy while maintaining a balance between energy efficiency and performance.
Finalization and Presentation
Finalization and Presentation plays a crucial role in the journey of creating a functional robot. This section serves as the culmination of all the hard work invested in designing and constructing the robot. The importance of this stage lies in presenting the robot in its polished form, ready to showcase its capabilities to the audience. It involves meticulous attention to detail to ensure that the robot not only functions effectively but also looks aesthetically pleasing, enhancing its overall presentation. Finalization and Presentation also provide an opportunity to document the entire process and showcase the evolution of the robot from concept to reality.
Documentation
Recording Design Process
Recording the design process forms the backbone of documenting the entire journey of creating the robot. It involves capturing every step taken, every decision made, and every modification implemented during the design phase. This documentation not only serves as a record of the robot's development but also offers valuable insights for future projects. The key characteristic of recording the design process is its ability to track progress, identify challenges faced, and ultimately, learn from mistakes. This meticulous documentation fosters a culture of continuous improvement, ensuring that each project builds upon past experiences.
Compiling Component Data
Compiling component data involves creating a comprehensive inventory of all the parts and components used in the construction of the robot. This meticulous cataloging serves multiple purposes, including facilitating future repairs or upgrades, ensuring compatibility of parts, and simplifying the troubleshooting process. The key characteristic of compiling component data is its role in enhancing the maintenance and longevity of the robot. By organizing component data systematically, it becomes easier to identify faulty parts, track usage patterns, and optimize the performance of the robot.
Creating User Manual
Creating a user manual is essential for providing users with clear instructions on how to operate the robot effectively. The user manual serves as a guidebook, outlining the functionalities, controls, troubleshooting steps, and safety precautions associated with the robot. The key characteristic of a user manual is its user-friendly design and comprehensive information, catering to users with varying levels of technical expertise. A well-crafted user manual not only enhances the user experience but also contributes to the overall functionality and longevity of the robot by promoting proper usage and maintenance.
Showcasing the Robot
Demonstrating Functions
Demonstrating the functions of the robot involves showcasing its capabilities and features in action. This hands-on approach allows viewers to witness the robot's performance firsthand, illustrating the culmination of all the effort put into its design and construction. The key characteristic of demonstrating functions is its ability to engage and captivate the audience, providing a tangible demonstration of the robot's practical applications. By showcasing the robot's functions, creators can highlight its unique selling points, versatility, and effectiveness in fulfilling its intended purpose.
Explaining Design Choices
Explaining the design choices made during the construction of the robot is essential for providing transparency and insight into the decision-making process. This involves rationalizing why specific components, configurations, or algorithms were chosen over others. The key characteristic of explaining design choices is its role in highlighting the critical thinking behind the design, emphasizing factors such as efficiency, cost-effectiveness, innovation, and user experience. By articulating the rationale behind design decisions, creators can offer a deeper understanding of the thought process that went into making the robot a functional reality.
Sharing Learnings
Sharing learnings involves reflecting on the challenges, successes, and lessons gleaned throughout the process of creating the robot. This knowledge-sharing initiative aims to impart valuable insights, best practices, and innovative approaches to fellow robotics enthusiasts. The key characteristic of sharing learnings is its collaborative nature, fostering a community of knowledge exchange and continuous improvement. By sharing experiences, experiments, and outcomes, creators can contribute to the collective growth and advancement of robotics technology, paving the way for future innovations and discoveries.
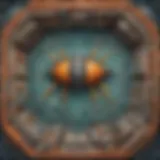
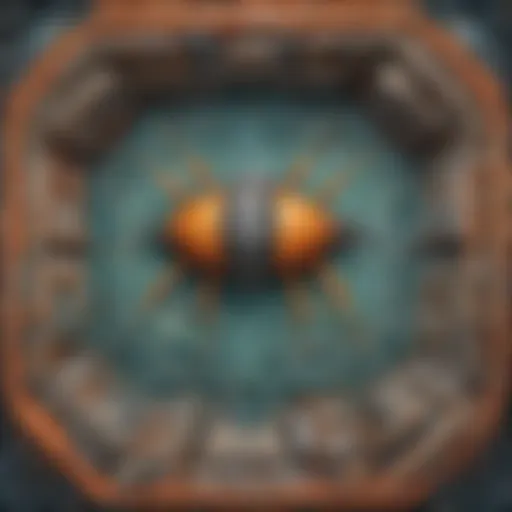