Unleashing the Mastery of Soldering for Circuit Boards: A Comprehensive Guide
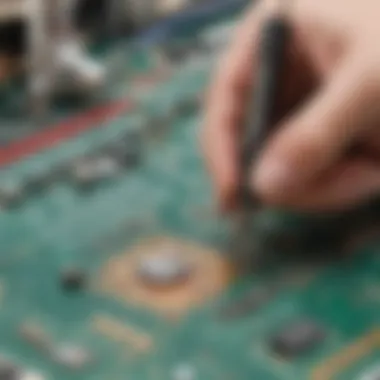
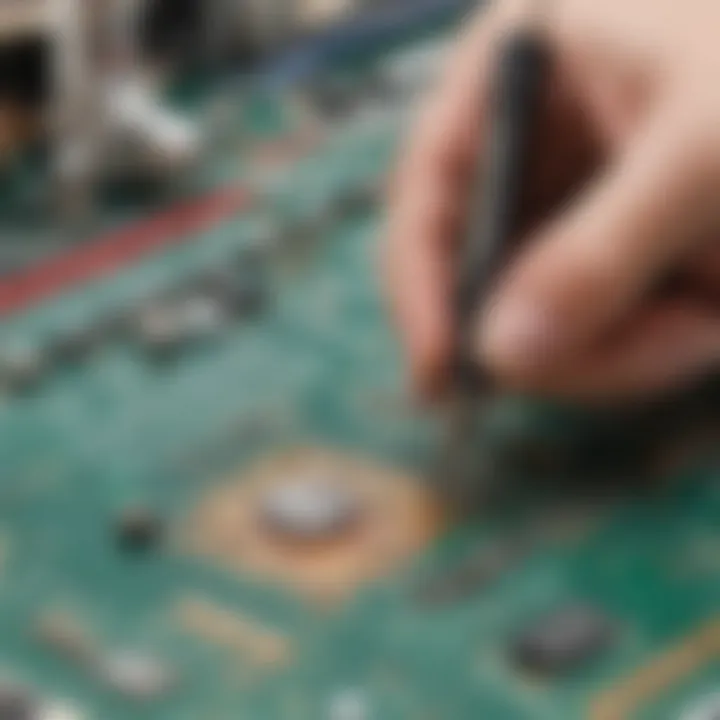
Science Fun Facts
Soldering, a crucial aspect of electronics, requires precision and attention to detail. Did you know that the process of soldering involves melting a filler metal to join metallic surfaces together? This fascinating technique is essential in creating reliable connections in circuit boards, ensuring optimal functionality. Soldering dates back to ancient times, where it was used in jewelry making and plumbing. The evolution of soldering techniques has paved the way for advancements in technology and innovation.
Discover the Wonders of Science
Exploring the realm of soldering unveils a world of scientific principles at play. From understanding the conductivity of metals to the thermal properties of solder alloys, soldering bridges the gap between theory and practical application. Educational videos illustrating soldering techniques provide valuable insights into the intricate process, allowing enthusiasts to grasp the artistry behind this essential skill. By delving into the real-life applications of soldering in everyday devices, individuals gain a deeper appreciation for the science behind electronics.
Science Quiz Time
Engage in a thought-provoking exploration of soldering through interactive quizzes and brain teasers. Test your knowledge on soldering tools, techniques, and safety precautions with multiple-choice questions designed to challenge and educate. Embrace the gamification of learning as you enhance your understanding of soldering fundamentals in a fun and interactive manner. Unravel the mysteries of soldering through engaging puzzles that reinforce key concepts and promote active learning.
Science Experiment Showcase
Embark on a soldering adventure with step-by-step instructions for fun and engaging experiments. Discover the materials list essential for soldering circuit boards and explore safety tips to ensure a secure and enjoyable experience. Dive into the world of precision and craftsmanship as you follow detailed guidelines for mastering the art of soldering. Enhance your skills while taking necessary precautions, fostering a safe and enriching environment for honing your soldering expertise.
Introduction
Soldering circuit boards is a fundamental skill in the realm of electronics, requiring precision and finesse. This critical process involves joining components to create functional circuits, making it an indispensable skill for novices and experts alike. Understanding the nuances of soldering not only ensures the reliability of electronic devices but also plays a significant role in the performance of these devices. In this article, we will delve into the intricate details of soldering, exploring the essential tools, techniques, and expert tips necessary for mastering precision in electronics.
Understanding Soldering
What is Soldering?
Soldering is a meticulous process that involves melting a filler metal to join two metallic surfaces together securely. This technique plays a pivotal role in electronics by creating conductive paths necessary for the functionality of circuit boards. The key characteristic of soldering lies in its ability to create robust electrical connections with high conductivity. This is a popular choice in electronics due to its efficiency in creating durable connections essential for the optimal performance of electronic components. Despite its meticulous nature, soldering's advantage lies in its ability to provide reliable connections, ensuring the smooth operation of electronic devices.
Importance in Electronics
Soldering holds immense significance in the realm of electronics as it is the foundation of circuit board assembly. The importance of soldering is underscored by its role in establishing electrical connections essential for the functionality of electronic devices. Its key characteristic lies in its ability to create stable and secure connections that withstand various operational conditions. This reliability makes soldering a popular choice in electronics manufacturing, ensuring the efficiency and longevity of electronic products. However, it is essential to note that improper soldering techniques can lead to faulty connections that compromise the functionality of electronic devices.
Types of Circuit Boards
Single-Sided Boards
Single-sided boards consist of a single layer of substrate with one conductive layer, making them suitable for simpler electronic applications. The key characteristic of single-sided boards is their cost-effectiveness and ease of manufacturing, making them a popular choice for basic electronic projects. Their unique feature lies in their simplicity, which offers a straightforward platform for electronic circuitry. However, the main disadvantage of single-sided boards is their limited circuit complexity, restricting their use in more advanced electronic applications.
Double-Sided Boards
Double-sided boards contain conductive layers on both sides of the substrate, providing more space for circuitry and components. The key characteristic of double-sided boards is their enhanced scalability, allowing for more complex circuit designs compared to single-sided boards. Their unique feature lies in the increased component density they offer, enabling the development of advanced electronic devices. However, the main disadvantage of double-sided boards is the complexity involved in manufacturing and troubleshooting, making them more challenging for beginners.
Multi-Layer Boards
Multi-layer boards consist of multiple layers of substrate with interconnected conductive layers, offering high circuit density. The key characteristic of multi-layer boards is their ability to support intricate circuit designs in compact form factors. Their unique feature lies in the optimized space utilization, allowing for the integration of diverse electronic components in a single board. However, the main disadvantage of multi-layer boards is the increased cost and complexity associated with their production, making them suitable for sophisticated electronic applications.
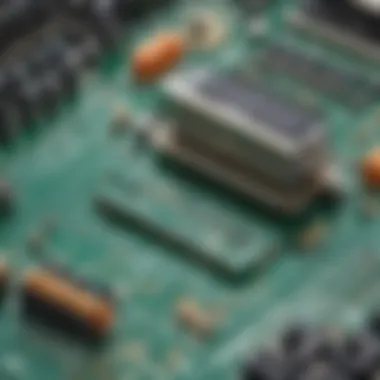
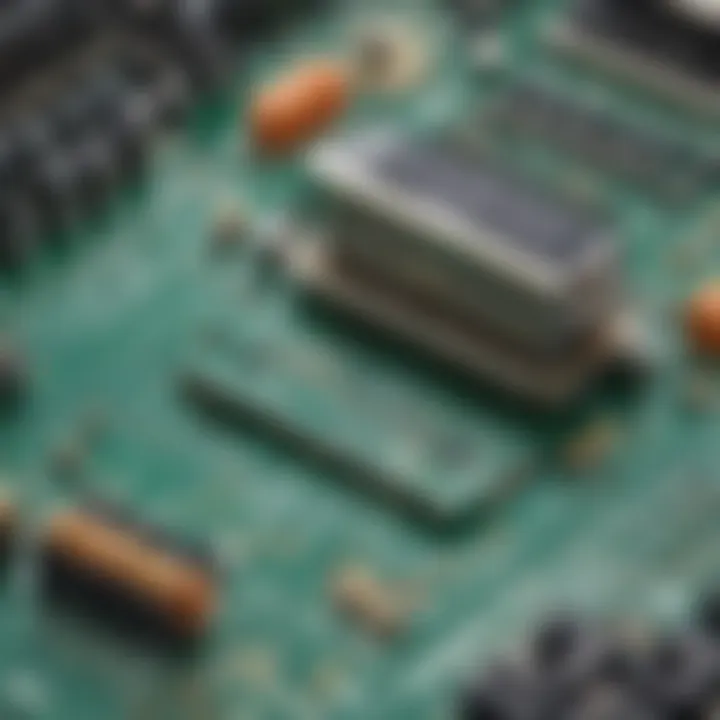
Essential Tools and Equipment
In the realm of soldering for circuit boards, understanding and utilizing essential tools and equipment is paramount. These tools are the backbone of any soldering endeavor, ensuring precision, efficiency, and quality in electronic assemblies. Soldering iron, solder wire, flux, solder wick, and flux remover are among the critical components that contribute to successful soldering processes. Each tool plays a unique role, from melting solder to cleaning excess flux. Choosing the right tools and equipment sets the foundation for impeccable solder joints and reliable circuit connections.
Soldering Iron
Types of Soldering Irons
Soldering irons come in various types, each tailored for specific soldering tasks. From pencil irons for intricate work to soldering stations for professional use, the array of soldering irons caters to diverse soldering needs. The wattage and tip design of soldering irons greatly influence the efficiency and precision of soldering. Selecting the appropriate soldering iron type is crucial for achieving optimal results in circuit board soldering. While some may prefer temperature-controlled irons for meticulous work, others may opt for standard irons for general soldering applications.
Choosing the Right One
Choosing the right soldering iron depends on factors like the intended use, soldering frequency, and project complexity. A soldering iron with adjustable temperature settings offers versatility and control over the soldering process. Additionally, considering the ergonomics and comfort of the soldering iron handle can enhance user experience during prolonged soldering sessions. It is essential to strike a balance between power output, heating element type, and tip compatibility when selecting a soldering iron to ensure efficient heat transfer and solder flow.
Solder Wire
Composition and Flux Core
Solder wire composition, characterized by the ratio of metals like tin, lead, and flux components, directly influences soldering performance. Flux core solder wire provides flux while soldering, facilitating better wetting and adhesion of solder to components. Choosing the right solder wire composition ensures robust solder joints and minimizes the risk of cold joints or insufficient bonding. The flux core plays a significant role in preventing oxidation and promoting solder flow, enhancing the reliability of solder connections.
Thickness and Diameter
The thickness and diameter of solder wire dictate the amount of solder delivered per solder joint. Thinner solder wires are suitable for delicate components and fine-pitch soldering, offering precise control over the soldering process. Conversely, thicker solder wires are ideal for high-current applications and larger components, ensuring sufficient solder volume for strong mechanical bonds. Selecting the appropriate solder wire thickness and diameter aligns with the component sizes and soldering requirements, optimizing joint quality and electrical conductivity.
Flux
Role in Soldering
Flux serves as a critical agent in soldering, promoting solder wetting and enhancing soldering quality. By removing oxides and contaminants from metal surfaces, flux facilitates the formation of strong metallurgical bonds between solder and components. The flux's activity levels and compatibility with solder alloys influence soldering outcomes, affecting joint appearance and reliability. Employing flux in soldering processes mitigates the risk of solder defects, such as cold joints or excess solder, ensuring consistent and durable solder connections.
Types of Flux
Different types of flux, such as rosin-based, water-soluble, and no-clean flux, cater to distinct soldering applications and requirements. Each flux type offers specific benefits and considerations concerning residue removal, application methods, and post-soldering cleaning. Understanding the characteristics and behavior of flux types helps in selecting the most suitable flux for specific soldering tasks. Whether seeking residue-free solder joints or seamless flux removal after soldering, choosing the appropriate flux type contributes to successful and reliable circuit board assemblies.
Solder Wick and Flux Remover
Purpose and Application
Solder wick and flux remover play pivotal roles in rework and repair tasks by facilitating the removal of excess solder and flux residues. Solder wick aids in absorbing surplus solder, correcting solder bridges, and desoldering components efficiently. Flux remover, on the other hand, ensures proper cleaning of soldered joints and PCB surfaces, eliminating flux residues that may compromise circuit performance or reliability. The combined use of solder wick and flux remover enhances the quality of soldering work, offering a clean and professional finish to circuit board assemblies.
Preparing for Soldering
In the intricate realm of soldering circuit boards, the preparatory phase holds paramount importance, akin to laying the foundation for a sturdy structure. The process of preparing for soldering serves as the bedrock upon which the success of soldered joints rests. It encompasses a series of meticulous steps and considerations that are indispensable for achieving optimal results in electronic assemblies.
One of the core elements of this preparatory phase involves cleaning the board to ensure a pristine working surface. An immaculately clean board is a prerequisite for achieving reliable soldered connections. Contaminants such as dust, oil residues, or flux remnants can impede the flow of solder and compromise the integrity of the joints. Therefore, meticulous attention to detail during the cleaning process is crucial for enhancing the overall quality and reliability of the soldering work.
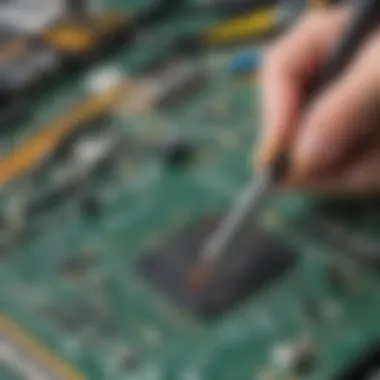
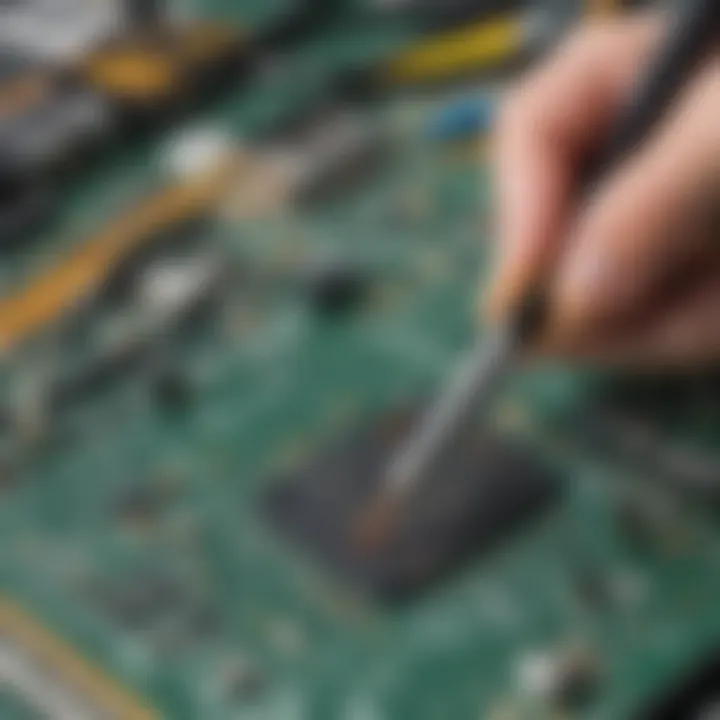
Component placement is another critical aspect of preparing for soldering, where strategic positioning plays a pivotal role in ensuring efficient workflow and optimal performance. By strategically placing components on the board in a systematic manner, soldering tasks can be streamlined, reducing the risk of errors and rework. Proper component placement also aids in minimizing the distance between components, thereby enhancing the overall compactness and functionality of the circuit board.
In addition to strategic positioning, avoiding heat damage is a key consideration during the preparation phase. Excessive heat exposure can lead to component failure, board delamination, or even irreversible damage. Therefore, implementing effective heat management strategies, such as using heat sinks, thermal barriers, or targeted heating techniques, is essential for safeguarding delicate components and preserving the integrity of the circuit board.
Soldering Techniques
Through-Hole Soldering
Steps for Through-Hole Components
The process of through-hole soldering involves specific steps that are integral to its success. From component placement to solder application, each step contributes to creating a robust connection between the component leads and the board. Understanding the nuances of through-hole soldering is crucial in achieving durable and efficient circuit assemblies. The key characteristic of through-hole components lies in their physical structure, which allows for secure anchoring and better heat dissipation. This aspect makes through-hole soldering a popular choice in industries where reliability and stability are paramount.
Pro Tips for Quality Joints
Achieving quality joints in through-hole soldering requires attention to detail and precision. Pro tips for quality joints include optimizing soldering iron temperature, ensuring proper solder flow, and inspecting joints for consistency. The distinctive feature of quality joints is their smooth and shiny appearance, indicating a strong and reliable connection. By following these pro tips, individuals can enhance the structural integrity of their solder joints and minimize the risk of electrical failures.
Surface Mount Soldering
Surface mount soldering presents unique challenges and solutions that are essential to understand for successful circuit board assembly. Overcoming obstacles such as small component sizes, tight spacing, and thermal management is paramount in surface mount soldering. The key characteristic of surface mount soldering lies in its compatibility with miniature electronic components, allowing for compact and lightweight circuit designs. Despite its challenges, surface mount soldering offers benefits in scalability and efficiency, making it a preferred choice in modern electronics manufacturing.
Challenges and Solutions
Navigating the challenges of surface mount soldering requires attention to detail and patience. Solutions involve using specialized tools like solder paste stencils, reflow ovens, and hot air rework stations to ensure precise component placement and solder reflow. The unique feature of surface mount soldering lies in its adaptability to automated assembly processes, streamlining production and reducing labor costs.
Reflow Soldering
Reflow soldering offers a methodical approach to soldering surface mount components, utilizing controlled heating and cooling cycles for optimal results. The key characteristic of reflow soldering is its ability to create reliable solder joints through the precise application of heat. This method provides advantages in terms of repeatability and consistency, ensuring uniform solder fillets and strong electrical connections. However, reflow soldering demands careful process control to avoid issues such as tombstoning and solder bridging.
Desoldering
Desoldering is a critical skill in electronics maintenance and repair, allowing for the removal of faulty components without damaging the circuit board. Mastering desoldering techniques requires dexterity and precision to extract components cleanly and efficiently. Strategies for desoldering range from using desoldering wicks to desoldering pumps, each offering a unique approach to component removal. The key characteristic of desoldering lies in its potential to refurbish circuit boards and salvage valuable components for reuse.
Techniques for Removing Components
Effective techniques for removing components involve heating the solder joints to their melting point and using tools to extract the component safely. Twisting and lifting, desoldering braid, and hot air rework stations are common methods employed in component removal. The unique feature of component removal techniques is their ability to disengage components from the board while minimizing thermal stress and mechanical damage.
Avoiding Damage to the Board
Avoiding damage to the board during desoldering is essential for preserving the integrity of the circuitry and preventing costly repairs. Techniques such as controlling temperature, applying localized heat, and using suitable desoldering tools contribute to avoiding board damage. The key characteristic of damage prevention methods is their focus on safeguarding delicate circuit traces and vias while removing components. By employing proper desoldering techniques, individuals can extend the lifespan of circuit boards and maintain their functionality over time.
Troubleshooting and Common Mistakes
Cold Joints and Bridges
Causes and How to Fi:
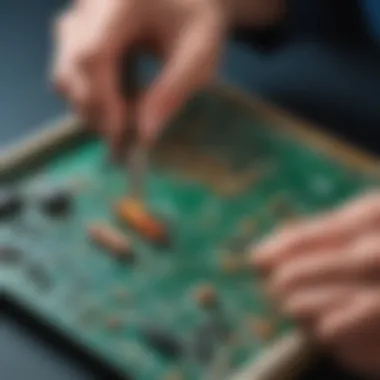
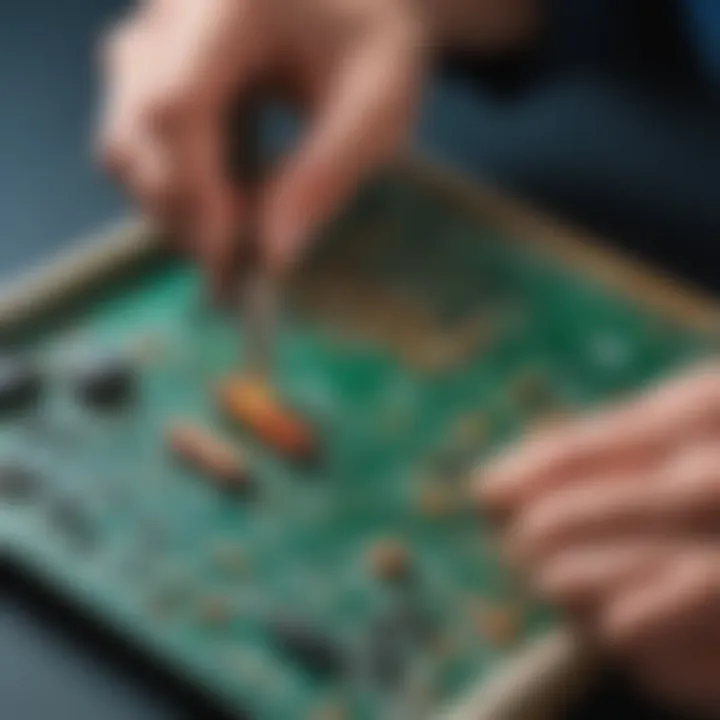
When discerning the causes and remedies for cold joints and bridges, a meticulous approach is necessary to pinpoint the underlying factors contributing to these issues. Cold joints typically arise from insufficient heat application during soldering, leading to incomplete solder flow and poor electrical connections. To remedy this, ensuring adequate heat transfer and sufficient dwell time during the soldering process is crucial. By meticulously inspecting the solder joints and reworking them as needed, a technician can rectify cold joints effectively. Addressing bridges involves the careful removal of excess solder that spans between two connections, which may lead to short circuits. Utilizing desoldering tools, such as solder wick, is instrumental in remedying bridges without causing damage to the circuit board.
Prevention Methdos:
Implementing preventative measures is key to avoiding the recurrence of cold joints and bridges in soldering work. Preheating the circuit board and components can aid in achieving optimal soldering temperatures, preventing the formation of cold joints. Furthermore, utilizing flux judiciously can enhance solder flow and prevent solder bridges by promoting proper wetting and adhesion. Conducting thorough visual inspections post-soldering to identify and address any potential cold joints or bridges proactively is essential in upholding soldering quality standards. By integrating these prevention methods into the soldering process, technicians can elevate the reliability and durability of circuit board connections.
Overheating Components
Navigating the challenges posed by overheating components is paramount in the realm of soldering for circuit boards, as excessive heat can jeopardize component integrity and functionality. Recognizing the symptoms and implementing suitable solutions is integral to preserving the overall quality of soldering work and safeguarding electronic devices against damage. Fostering an adept understanding of protection techniques further fortifies technicians against the adverse effects of overheating, underscoring the significance of precision and caution in soldering endeavors.
Symptoms and Soluitons:
Identifying symptoms of overheating components is critical to prompt intervention and mitigation. These symptoms may manifest as discoloration, component deformation, or even electronic malfunctions. To address overheating effectively, technicians can employ techniques such as heat sinks, thermal insulation materials, and controlled soldering temperatures. By leveraging these solutions, the adverse effects of overheating can be ameliorated, ensuring the longevity and reliability of soldered components. Prioritizing thermal management in soldering operations is key to preempting overheating-related issues and upholding the integrity of electronic assemblies.
Protection Techniqeus:
Employing robust protection techniques serves as a bulwark against the perils of overheating in soldering applications. Encapsulating sensitive components with thermal shielding materials, regulating soldering iron temperatures, and maintaining proper ventilation are cornerstone strategies in safeguarding against component damage due to excessive heat. By integrating these protection techniques into the soldering process, technicians can mitigate the risks associated with overheating, fostering a secure operational environment for electronic devices. Upholding stringent quality control measures and adhering to best practices in thermal management are imperative in fortifying the resilience of soldered components against thermal stresses and ensuring enduring performance.
Advanced Tips and Best Practices
Amping up your skills in soldering is of paramount importance when aiming for excellence in handling circuit boards. Advanced tips and best practices play a crucial role in refining your techniques to ensure optimal performance. Navigating through the intricacies of lead-free soldering is a key area that demands attention. Understanding the benefits and considerations associated with this technique is essential. Lead-free soldering presents a safer alternative compared to traditional lead-based options. The environmental advantages of lead-free soldering are notable, aligning with the industry's push towards eco-friendly practices. However, it is crucial to consider the higher melting points and potential brittleness of lead-free solder when implementing this technique. Adapting to changing industry standards is another critical aspect that must not be overlooked. Keeping abreast of the latest trends and regulations in soldering practices is vital for maintaining quality and compliance. Embracing new industry standards ensures that your soldering processes are in line with advancements and best practices, setting you apart as a competent professional in the field.
Lead-Free Soldering
Benefits and Considerations
Delving deeper into the realm of lead-free soldering unveils a myriad of benefits that this technique offers. One of the primary advantages is the reduction of harmful lead exposure, promoting a safer working environment for practitioners. The absence of lead in solder joints eliminates health risks associated with lead poisoning, safeguarding both the individuals directly involved in the soldering process and the environment. Additionally, lead-free soldering aligns with global environmental regulations, contributing to sustainable and environmentally conscious practices. However, it's essential to be mindful of certain considerations when opting for lead-free soldering. One key aspect to note is the relatively higher melting point of lead-free solders, which may require adjustments in soldering techniques and equipment. Ensuring compatibility with lead-free solders while considering the impact on component longevity and reliability is crucial for successful implementation.
Changing Industry Standards
As the technology landscape evolves, so do industry standards surrounding soldering practices. Adapting to these dynamic shifts is imperative for professionals seeking to excel in circuit board assembly. One prominent aspect of changing industry standards is the emphasis on eco-friendly and sustainable soldering solutions. The move towards lead-free soldering aligns with broader initiatives to reduce environmental impact and promote responsible manufacturing processes. By embracing changing industry standards, individuals and organizations demonstrate a commitment to quality, safety, and environmental stewardship. Integrating these standards into soldering practices not only ensures compliance with regulatory requirements but also positions practitioners at the forefront of industry advancements, enhancing reputability and credibility.
Soldering in Sensitive Areas
ESD Precautions
Within the domain of soldering, Electrostatic Discharge (ESD) precautions are paramount when working in sensitive areas. The delicate nature of electronic components necessitates stringent measures to prevent ESD-related damage. Implementing ESD precautions involves creating an electrostatically safe working environment to mitigate the risk of static discharge. By utilizing ESD-safe workstations, grounding straps, and antistatic packaging, practitioners can safeguard sensitive components from ESD-induced failures. The key characteristic of ESD precautions lies in their proactive approach to preventing latent damage caused by electrostatic discharge. While ESD precautions offer significant protective benefits, it's essential to recognize the limitations of such measures and exercise caution to ensure comprehensive protection of sensitive components.
Handling Delicate Components
Effectively managing delicate components during soldering processes requires finesse and precision to prevent damage and ensure operational integrity. The key characteristic of handling delicate components lies in the meticulous attention to detail and gentle touch required throughout the process. By employing specialized tools such as fine-tipped tweezers, vacuum pick-up tools, and magnification devices, practitioners can manipulate delicate components with accuracy and care. Handling delicate components involves strategic placement, accurate positioning, and secure attachment to guarantee optimal functionality post-soldering. While the unique features of delicate component handling enhance precision and accuracy in soldering tasks, practitioners must also be aware of the fragility of these components and exercise caution to avoid stress-induced failures.
Quality Control and Testing
Inspection Methods
Ensuring the reliability and functionality of soldered joints necessitates thorough inspection methods that scrutinize the integrity of connections. Inspection methods encompass visual examination, X-ray inspection, and automated optical inspection to detect issues such as cold joints, misalignment, and insufficient soldering. The key characteristic of inspection methods lies in their ability to identify defects and discrepancies that may compromise circuit board performance. By integrating comprehensive inspection protocols into soldering processes, practitioners can maintain quality standards and rectify issues promptly to prevent potential malfunctions.
Functional Testing
Validating the functionality and performance of soldered components through rigorous functional testing is imperative to guarantee operational efficiency. Functional testing involves subjecting circuit boards to simulated operational conditions to assess their adherence to design specifications and functionality requirements. The key characteristic of functional testing lies in its ability to replicate real-world usage scenarios, allowing for the identification of defects and performance issues. By conducting thorough functional testing procedures, practitioners can identify and rectify any functional deviations, ensuring that soldered components meet functional expectations and performance standards.