Mastering the Art of DIY Fabric Printing: A Comprehensive Guide
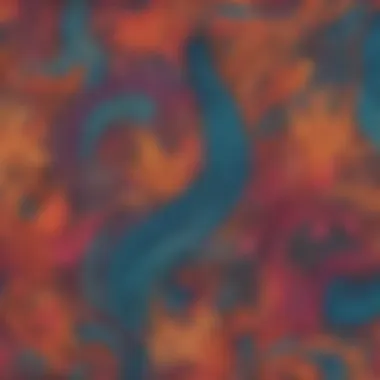
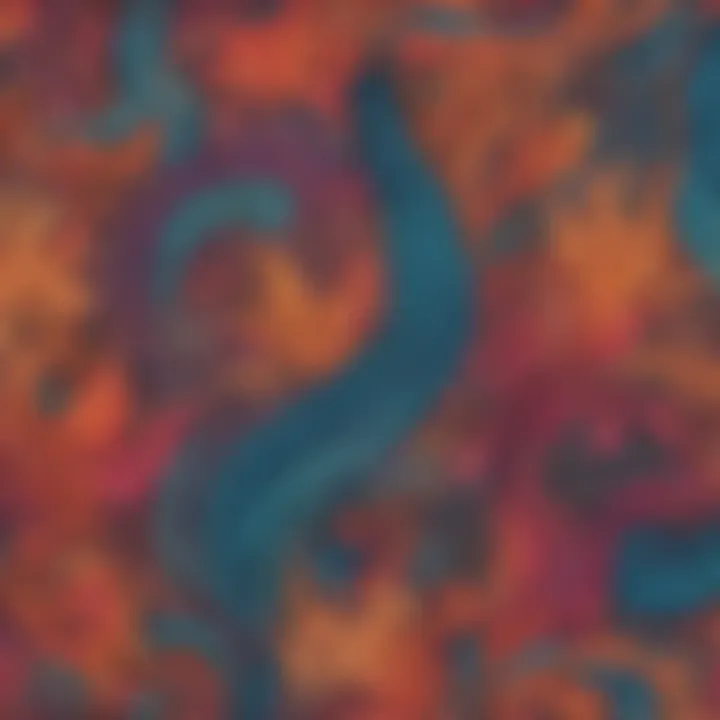
Science Fun Facts
Fabric printing has a rich history that dates back centuries. Did you know that different cultures around the world have their unique textile printing techniques? From traditional block printing in India to batik dyeing in Indonesia, the art of fabric printing reflects the diverse creative expressions of humanity. Understanding these traditional methods can inspire contemporary fabric printing projects to blend heritage with innovation.
Discover the Wonders of Science
When delving into the realm of fabric printing, we encounter a fascinating interplay of chemistry and art. The selection of dyes and pigments involves understanding the chemical properties that make colors vibrant and lasting on various types of fabric. Exploring how different chemicals interact with fabric fibers unveils the scientific principles behind achieving precise hues and patterns in DIY fabric printing. By grasping these scientific concepts, aspiring fabric printers can optimize their creative process for exceptional results.
Science Quiz Time
Let's spice up our fabric printing journey with a quiz! Test your knowledge on the history of fabric printing, the origins of different printing techniques, and the impact of modern technology on this ancient craft. Challenge yourself with brain teasers like identifying the primary colors used in fabric printing or unraveling the sequence of steps in the screen printing process. Embark on a fun and educational quiz to deepen your understanding of fabric printing while honing your critical thinking skills.
Science Experiment Showcase
Welcome to the fabric printing laboratory! Prepare your materials and safety gear as we delve into the exciting realm of DIY fabric printing experiments. Follow step-by-step instructions to create your custom designs using innovative printing techniques. Discover how simple household items like potatoes or sponges can transform into printing tools, unlocking endless possibilities for artistic expression. Stay safe by adhering to precautionary measures and let your imagination soar in this hands-on fabric printing showcase.
Introduction
Understanding Fabric Printing
History of 'Fabric Printng'
The historical evolution of fabric printing is a captivating narrative that bridges the past with the present. From ancient techniques rooted in tradition to modern innovations driven by technological advancements, the history of fabric printing is a tapestry of creativity and craftsmanship. Exploring this historical backdrop not only provides insights into the roots of textile design but also inspires contemporary artists to draw from a rich legacy of printmaking techniques. The interplay between tradition and innovation in fabric printing serves as a testament to the enduring appeal and versatility of this age-old craft.
Benefits of Printing Your Own Fabric
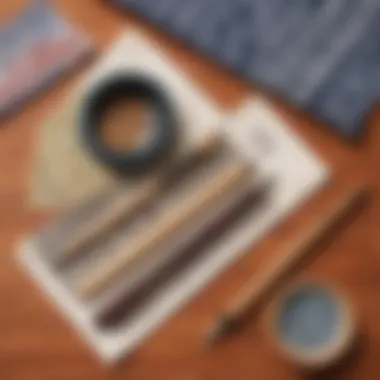
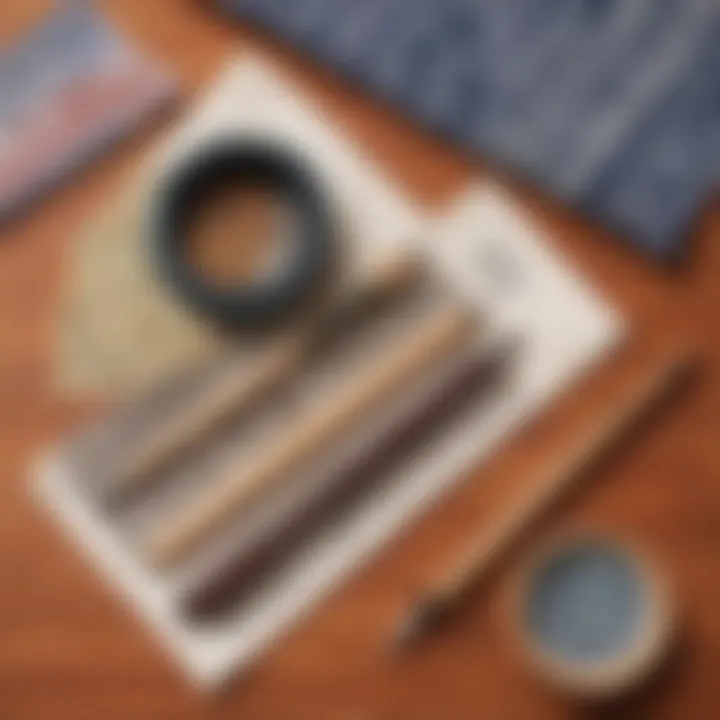
The ability to print your own fabric offers a myriad of advantages that extend beyond mere customization. By taking control of the design process, individuals can express their unique style and personality through original creations. Printing your own fabric allows for unparalleled creative freedom, enabling artists to experiment with colors, patterns, and textures to achieve truly bespoke results. Moreover, DIY fabric printing promotes sustainability by encouraging the reuse of materials and reducing waste, making it a socially conscious and environmentally friendly choice.
Impact of Technology on Fabric Printing
Technology has revolutionized the field of fabric printing, ushering in a new era of possibilities and capabilities. Advancements in digital printing technologies have democratized the design process, making complex patterns and intricate details accessible to a wider audience. The integration of technology in fabric printing has streamlined production processes, allowing for greater efficiency and precision in textile design. By harnessing the power of technology, fabric printers can push the boundaries of creativity and innovation, pushing the art form to new heights.
Materials Needed
Types of Fabrics Suitable for Printing
Selecting the right fabric is paramount to the success of any printing project. Different fabrics possess unique characteristics that can affect the outcome of the print, from the texture and weight of the material to its absorbency and drape. Understanding the properties of various fabrics is essential in choosing the appropriate base for your designs, ensuring optimal results that align with your creative vision.
Ink and Dye Options
The selection of ink and dye is a critical decision that influences the vibrancy, durability, and overall quality of the printed design. Different inks and dyes offer distinct advantages and limitations, from water-based inks that provide a soft hand feel to pigment dyes that offer superior color fastness. By exploring the diverse range of ink and dye options available, fabric printers can tailor their choices to suit specific project requirements and achieve desired aesthetic outcomes.
Essential Tools and Equipment
Equipping oneself with the necessary tools and equipment is essential for a seamless fabric printing process. From basic supplies like screens and squeegees for screen printing to specialized tools for block printing and digital printing, having the right equipment at hand can significantly enhance efficiency and precision. Moreover, investing in quality tools ensures consistency and accuracy in printing, leading to professional-quality results that stand the test of time.
Preparation
Washing and Preparing the Fabric
A crucial step in the fabric printing process, washing and preparing the fabric sets the foundation for successful prints. Pre-treating the fabric ensures optimal ink absorption and color retention, preventing bleed and fading. Understanding the specific requirements of each fabric type, from natural fibers like cotton to synthetic fabrics like polyester, is key to achieving desired results. By meticulously preparing the fabric surface, printers can ensure that their designs adhere flawlessly and maintain their integrity wash after wash.
Design Considerations
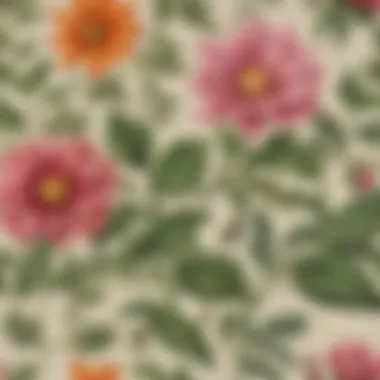
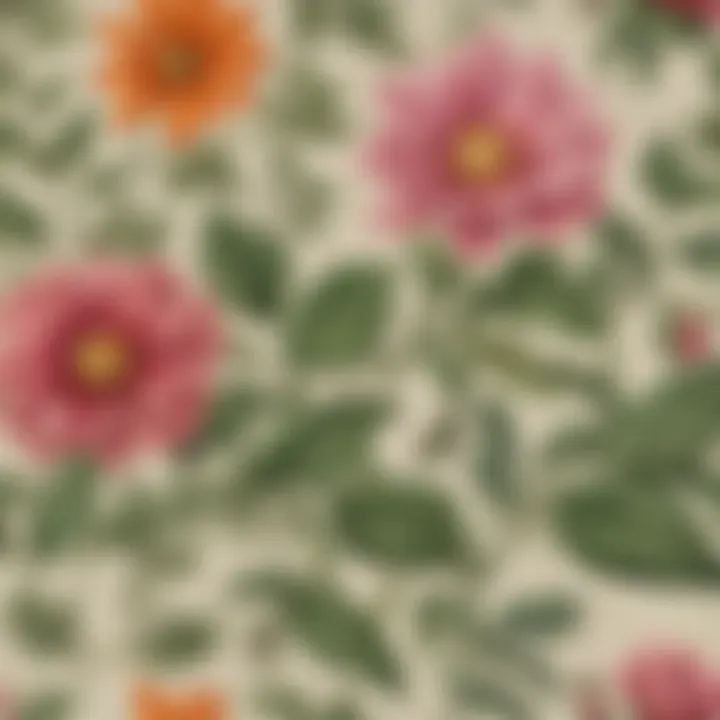
Developing a thoughtful and cohesive design is central to the fabric printing process. Considering elements such as color palettes, motifs, and scale is essential in creating visually striking prints that resonate with the intended audience. Whether drawing inspiration from nature, art, or personal experiences, designers must pay attention to detail and composition to bring their vision to life on fabric. By honing their design skills and thoughtfully planning each print, fabric printers can craft exquisite textiles that captivate and inspire.
Printing Techniques
Combining traditional craftsmanship with modern innovation, various printing techniques offer distinct approaches to translating designs onto fabric. From the meticulous patterns of block printing to the intricate details of screen printing and the versatility of digital printing, each technique presents unique strengths and considerations. Hand painting, with its artisanal charm and handcrafted appeal, offers a more hands-on approach to fabric customization. By understanding the nuances of each printing method, fabric printers can leverage diverse techniques to achieve desired effects and elevate their designs.
Step-by-Step Guide
Creating a Design
The design stage is where creativity flourishes and ideas manifest into tangible forms. Whether sketching by hand or designing digitally, capturing the essence of a concept and translating it into a visual representation is a pivotal step in the printing process. Taking into account factors such as repeat patterns, color variations, and placement on the fabric is essential for creating balanced and visually appealing designs. By investing time and effort in crafting well-thought-out designs, fabric printers can produce prints that resonate with aesthetic and artistic excellence.
Preparing the Printing Surface
Ensuring a smooth and clean printing surface is essential for achieving crisp and precise prints. Properly prepping the printing surface, whether using screens, blocks, or digital interfaces, involves thorough cleaning and calibration to eliminate any imperfections or contaminants that may affect the print quality. By meticulously preparing the printing surface, printers can guarantee sharp and accurate transfers of their designs onto fabric, resulting in flawless and professional-looking prints.
Printing the Fabric
The printing stage is where the magic happens, transforming blank fabric into vibrant canvases of expression. Executing the printing process with precision and care is crucial for achieving consistent and top-quality results. Whether using manual techniques like block or screen printing or digital methods for intricate designs, paying attention to pressure, ink application, and registration is key to producing flawless prints. By taking the time to master printing techniques and refine their skills, fabric printers can create products that exude craftsmanship and attention to detail.
Bit Creating Mistake or Duplicating
Setting the Print
After printing, setting the ink is essential to ensure durability and color fastness. Properly curing the print through heat setting or other techniques enhances the longevity and washability of the design, ensuring that it withstands the test of time. Factors such as temperature, pressure, and duration of setting play a crucial role in securing the print onto the fabric, enhancing its resistance to fading or washing out. By carefully setting the print, fabric printers can confidently showcase their designs with the assurance of lasting quality and vibrancy.
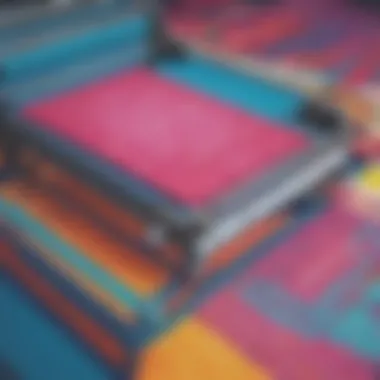
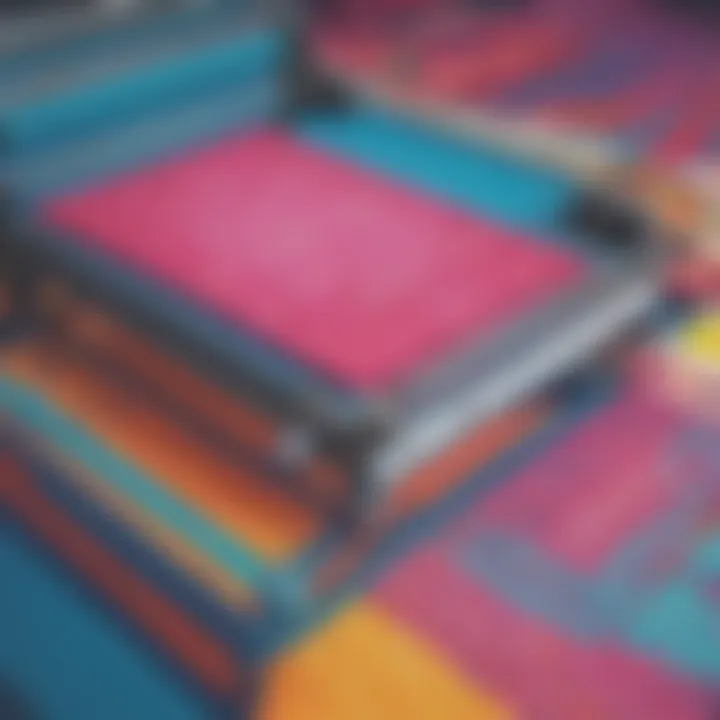
Finishing Touches
Drying and Curing
Following the printing process, thorough drying and curing of the fabric guarantee the longevity and resilience of the print. Allowing the ink to fully dry and cure prevents smudging or bleeding, ensuring that the design retains its integrity and clarity. Harnessing proper drying techniques and adhering to curing recommendations for specific inks are instrumental in preserving the quality of the final product. By exercising patience and diligence in the drying and curing phase, fabric printers can produce prints that withstand the test of time and wear.
Ironing and Care Instructions
Once the print has fully set, ironing and providing care instructions for the finished fabric are paramount for maintaining its appearance and quality. Properly ironing the fabric on the reverse side with a suitable heat setting preserves the print and enhances its visual appeal. Furthermore, offering clear care instructions to end-users, such as washing recommendations and storage tips, ensures that the fabric retains its beauty and longevity over time. By emphasizing proper care and maintenance practices, fabric printers can empower consumers to enjoy their creations for years to come.
Advanced Tips
Experimenting with Color Mixing
Pushing the boundaries of color mixing opens a world of creative possibilities in fabric printing. By exploring various color combinations, gradients, and effects, fabric printers can create remarkable and unique designs that captivate the eye. Experimenting with color mixing techniques, such as shading, blending, and color blocking, allows for innovative and dynamic prints that showcase mastery of color theory and application. By embracing experimentation and fearlessly blending hues, fabric printers can unlock infinite design potentials and set their creations apart.
Incorporating Textures
Integrating textures into fabric prints adds depth, tactility, and visual interest to the designs. By incorporating textural elements like raised surfaces, embossing, or faux finishes, fabric printers can elevate their prints from two-dimensional patterns to multidimensional artworks. Textures enhance the tactile experience of fabrics, inviting touch and exploration beyond visual appeal. By skillfully blending textures with colors and patterns, fabric printers can create rich and engaging designs that beckon admiration and intrigue.
Layering Techniques
Layering techniques in fabric printing offer a dynamic approach to creating depth and complexity in designs. By superimposing multiple layers of prints, colors, or textures, fabric printers can achieve intricate and visually stunning outcomes that reflect a sophisticated understanding of composition and aesthetics. Layering opens up endless possibilities for experimentation and customization, allowing artists to craft multifaceted and nuanced prints that tell compelling stories. By mastering layering techniques, fabric printers can push the boundaries of creativity and craft one-of-a-kind textiles that resonate with depth and intricacy.
Troubleshooting
- [ Dealing with Smudging or Blurring]: Sometimes prints may suffer from smudging or blurring, detracting from the overall quality of the design. Implementing proper drying and curing techniques, adjusting ink consistency, and ensuring optimal pressure during printing can help mitigate issues of smudging and blurring, preserving the sharpness and clarity of the print.
- [ Fixing Ink Bleed]: Ink bleed can mar the crispness of a print, leading to unwanted spreading or feathering of colors. To address ink bleed, adjusting ink viscosity, controlling temperature and humidity levels during printing, and utilizing proper drying and setting methods can prevent excessive ink diffusion and maintain the integrity of the design.
Inspiration and Ideas
Fabric printing offers a boundless realm of inspiration and ideas for creative exploration. Exploring different themes, from floral motifs to geometric patterns, allows artists to infuse their designs with narrative and symbolism, bringing depth and meaning to their prints. Leveraging design resources for inspiration sparks innovative ideas and facilitates the development of unique concepts that resonate with personal style. Personalizing prints with elements that reflect individuality and emotion adds a personal touch to designs, creating a connection between the creator and the audience.
Inspiration, combined with practical knowledge and technical proficiency, fuels the fabric printing journey, propelling creators towards new horizons and exciting possibilities. Reflecting on one's achievements and learnings from the printing process informs future projects and explorations, guiding fabric printers towards continued growth and excellence in their craft. By embarking on this transformative journey of creativity and self-expression, artists can unlock their full potential and leave a lasting imprint on the world of textile design.