Understanding the Mixture of Sand and Cement in Construction
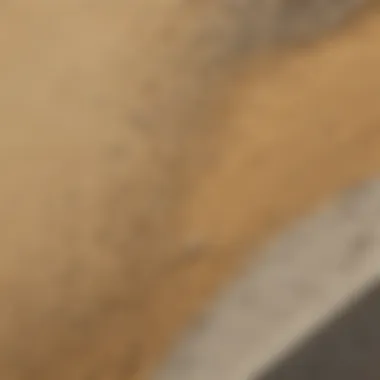
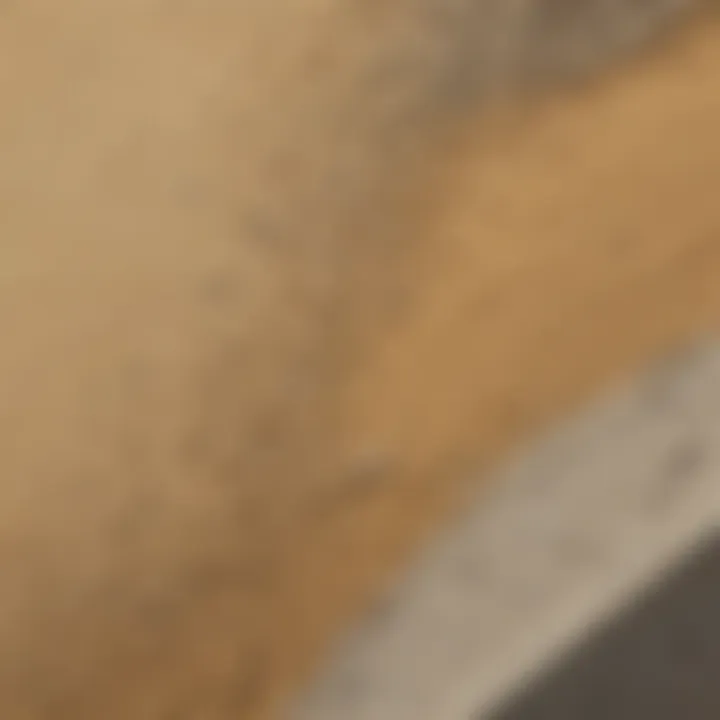
Intro
The combination of sand and cement is a cornerstone of construction projects. This mixture plays a vital role in creating strong, durable structures. Understanding the science behind this combination is essential for engineers, builders, and even curious minds. In this article, we will explore the fundamental components, ideal ratios, and ways to effectively mix sand and cement.
Science Fun Facts
- Cement Hydration: When water is added to cement, a chemical reaction occurs called hydration, which solidifies the material over time.
- Silica in Sand: Sand is mostly made up of silica, which contributes to the strong bond when combined with cement.
- Temperature Effects: The temperature can affect the strength of the mixture. For instance, colder weather can slow down the curing process, while hot weather can make the mixture dry too quickly.
Proper understanding of materials is key to successful construction.
Properties of the Mixture
Knowing the properties of the sand and cement mixture helps optimize it for various applications. The consistency affects how well the mixture can bind, how workable it is, and ultimately, how strong the end product will be.
Sand and cement together can yield different textures, from very fine for smoother surfaces to coarser for more robust constructs. Understanding variables like water content can significantly influence the strength of final disease and longevity.
Ideal Ratios
Different construction projects may require different proportions of sand and cement. Commonly, a ratio of around 3:1 of sand to cement is standard for many applications like concrete. For mortar used in bricklaying, ratios can be more variable, such as 1:4 of cement to sand. Adjusting these ratios based on environmental factors and desired strength is necessary.
Mixing Techniques
Mixing sand and cement correctly is important to achieve desired results. Here are some techniques:
- Dry Mixing: Combines the dry sand and cement before adding water.
- Wet Mixing: Involves adding water slowly to the mixture until reaching optimal consistency.
- Mechanical Mixing: Utilizing tools like concrete mixers for larger quantities ensures even distribution.
Troubleshooting Common Issues
Even experienced builders can face challenges with mixing sand and cement. Some common issues are:
- Cracking: This can occur if the mixture dries too quickly or has inadequate water. Make sure to maintain proper moisture during curing.
- Weak Bonds: Not achieving the right mixing ratio can weaken the bond. Test your mixtures on small scales before large projects.
- Excess Water: Too much water can dilute the bonds forming in the cement, leading to instability over time.
Prologue to Sand and Cement
The blend of sand and cement serves as a cornerstone in construction. Its significance cannot be overstated, as it influences not just the strength but the durability of various structures. Understanding this mixture involves each component's role, taking into account the effects of the mixing process and the practical applications. This knowledge is valuable not only to professionals in the field but also to educators and students learning about practical material science.
Definition of Sand and Cement
Sand is a granular material composed of finely divided rock and mineral particles. It primarily comes in categories like fine sand and coarse sand, which influences the concrete's final texture and strength. Cement acts as a binding agent, typically made from limestone and clay, when mixed with water. It hydrates and sets over time, creating a solid matrix that stabilizes the other materials. Both sand and cement are essential for creating various mixtures in construction, ensuring the needed resilience and longevity.
Historical Context
The history of combining sand and cement dates back to ancient civilizations. The Romans pioneered the use of a form of concrete that includes this mixture more than two thousand years ago. They utilized volcanic ash, which reacted with lime to yield a strong, durable substance. In modern construction practices, innovations have led to different formulas for mixing sand and cement, but the fundamental principles remain intact. This evolution in methods highlight a continued relevance in building practices. Understanding this history adds layers to how today’s mixtures are formulated, ensuring quality and safety in every structure built.
“Construction has always been an interplay between innovation and tradition.”
By grasping these foundational elements, individuals gain insights into the functionality and significance of sand and cement in both historical and contemporary contexts. Together, they maintain a vital presence in the world of construction.
The Role of Sand in the Mixture
The role of sand in the mixture of cement and sand holds substantial significance. Sand acts as an aggregate that adds volume and stability to concrete. Its texture and size affect how the mixture performs during curing and in the final application. The quality of sand is just as critical as that of cement. A poor-quality sand can lead to decreased strength and durability while affecting workability.
While working on construction projects, one must carefully select the type and properties of sand used in the mixtures. Furthermore, understanding the role sand plays can help in achieving the desired outcomes. Sand influences different aspects, including strength, durability, and overall quality of constructed structures.
Types of Sand Used
Various types of sand are used in concrete and mortar mixtures. One will typically hear terms like fine sand, coarse sand, and synthetic sand. Free from impurities, materials like crushed granite and limestone are popular choices.
- Fine Sand: This sand has smaller particles and is ideal for creating smooth surfaces in concrete or for use in mortar mixtures.
- Coarse Sand: Coarser variants provide better drainage and strength when mixed with cement. This type can enhance the mechanical properties of concrete.
- Crushed Sand: Also known as manufactured sand, crushed sand is produced by pulverizing stone and rocks. This sand often encourages better strength in the final concrete.
The suitability of each type comes from the project's needs. The function of the mixture can entirely change based on the type of sand used. Thus, understanding these differences helps in making informed decisions for construction needs.
Properties of Sand
Sand possesses several properties that contribute to how it reacts in mixtures. Some key properties are texture, gradation, and moisture content.
- Texture: The surface characteristics of sand particles influence how well they bond with cement. Rough textures provide better interlocking and strength, while smoother textures give more fluidity to the mixture.
- Gradation: This refers to the size distribution of sand particles. Well-graded sand includes different sizes. It aids in improved packing, reducing voids, and leading to a denser mixture.
- Moisture Content: The water retained in the sand affects the entire mixture. The balance is essential; too much moisture can make for a sloppy mixture, while too little stops cement from adequately wetting the sand, impairing binder formation.
Cement: The Binding Agent
Cement plays a crucial role in the sand and cement mixture. It is more than just a powder; it acts as the bond holding together the other materials in the mix. This binding quality defines the overall strength and durability of the resultant concrete or mortar used in various applications.
The significance of cement cannot be overstated. Its unique properties allow it to set and harden after being mixed with water, seamlessly integrating with sand and aggregates. This reaction, called hydration, ensures the mixture develops the required load-bearing capabilities.
Cement also contributes to various characteristics of the mixture such as workability and set time. Selecting the right type of cement is essential in achieving optimal results in construction projects. In this way, understanding cement and its contributions is vital for anyone involved in building practices.
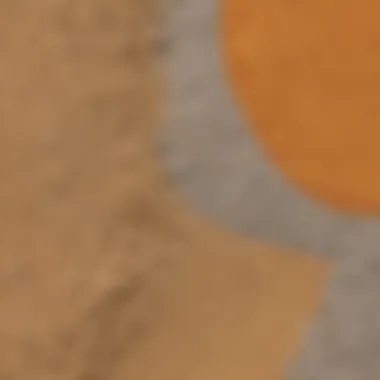
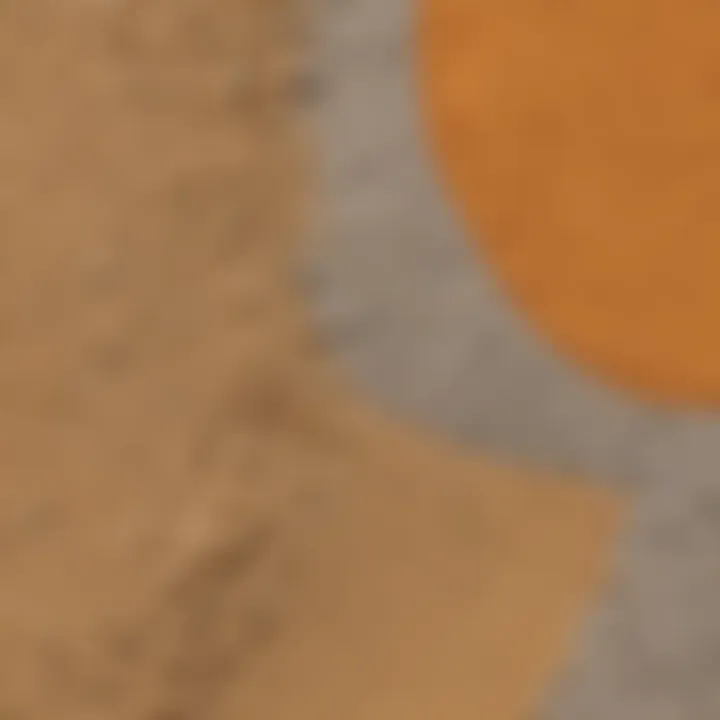
Types of Cement
There are several types of cement used in construction, each adapted for various environments and construction methods. Here are some common types:
- Portland Cement: Most widely used. It provides durability and strength.
- Blended Cement: This type includes a mixture of materials like fly ash. It helps reduce environmental impact.
- Rapid-Setting Cement: Cures quickly, ideal for urgent repairs.
- White Cement: Employed for architectural designs seeking a clean look.
- Oil Well Cement: Designed for high-pressure environments in oil extraction.
Each type of cement brings a different set of properties and capabilities which influences the choice depending on the specific demand of the construction task.
Chemical Composition of Cement
The chemical makeup of cement is intricate and critical. Cement is primarily composed of:
- Calcium Silicates: Fosters strength and durability.
- Alumina: Affects the speed of setting time.
- Iron Oxide: Contributes color and strength directly.
- Calcium Sulfate: Regulates the setting properties and workability.
These components interact chemically when mixed with water in the hydration process. The exact ratios of these elements will determine specific attributes of the finished mix. Different applications might require a careful adjustment of these compositions to meet their unique performance specifications.
Cement acts as the soul of concrete, defining its properties and support under loads. Understanding cement is vital for every builder.
For specialists in material science and those engaged deeply in construction, deeper knowledge about cement composition helps in aligning the outcomes with the expectations set for safety and building longevity.
Mixing Ratios and Techniques
Mixing ratios are essential in the preparation of sand and cement mixtures. Understanding these ratios dictates the strength and durability of the final product. The right balance results in structures capable of withstanding varying weights and environmental conditions. This section covers the significance of proper mixing ratios, along with techniques that help achieve optimal results for different uses.
Standard Mixing Ratios
The standard mixing ratio is important for achieving the desired consistency and strength in concrete and mortar. Generally, the most common ratios are:
- Concrete: A common ratio for standard concrete is 1 part cement, 2 parts sand, and 4 parts gravel. This is often expressed as a simpler notation, like 1:2:4.
- Mortar: For mortar, typically used in bricklaying, the ratio is often 1 part cement to 3 parts sand, presented as 1:3.
These ratios provide a base directory but depending on the exact project or location, adjustments may enhance the final mixture.
Moreover, the type of cement or quality of sand may require different ratios. For example, using high-strength concrete may necessitate additional cement. It's also important to remember that water affects the ratio balance as well. The inclusion and quality of water are key to getting the proper consistency and workability.
Therefore, verification through testing can assure proper performance based on desired load forecasts and application conditions.
Adjusting Ratios for Specific Applications
Different construction purposes necessitate adjustments in the traditional ratios. Here are some applications where specific ratios might differ:
- Pavements often use a lower water-to-cement ratio, since it reflects strength rather than workability. A ratio of 1:1.5:3 helps to achieve this.
- Waterproofing structures usually benefit from higher proportions of cement to minimize porous paths. In this case, a 1:2.5 sand-to-cement ratio may be adopted.
- Fast-setting mixtures require a different interaction, often utilizing additives for a higher cement ratio near 1:2 composition for quicker hardening.
When making these adjustments, one must consider:
- Climate conditions: Weather can affect the drying process. A humid environment can slow down curing.
- Aggregate type: The gravel or stone will dictate other elements in your mix and alter runtime and performance.
- Load bearing requirements: Max-load structures will need additional strength nuance reflect in mixing ratios.
In practical work, verifying via trials or tests prior to large-scale application is recommended. This reduces the risk of structural failure or premature cracking.
A proper understanding of mixing ratios and adjustments is vital to all stages of construction, influencing the relationship between strength and performance over time.
Water: A Critical Element
Water is an often underappreciated yet essential component of the sand and cement mixture. The right amount of water influences the overall strength and durability of the concrete. Without effective water management, it is difficult to achieve the optimal properties required for construction. Not only does water facilitate the mixing process, but it also plays a significant role in the hydration reaction crucial for setting the cement.
Importance of Water in the Mixture
Water serves various critical functions in the sand and cement mixture. Here are some key points to consider:
- Hydration: Cement needs water to activate its chemical processes. Hydration creates bonds that harden the mixture, forming strong concrete.
- Fluidity: Water aids in achieving the ideal consistency. A mix that is too dry can lead to poor workability, while too much water can create a soupy mass that is hard to control.
- Curing: After mixing, water is essential in curing the concrete. Continued hydration assists in the long-term strengthening process, giving it time to become robust and resistant to wear over time.
Notice that water quality is important too. Using clean, drinkable water is best. Contaminated water can impact the performance of the mixture negatively.
Effects of Water Content on Strength
The amount of water in a mixture has a direct relationship with its final strength.
- Low Water-to-Cement Ratios: Lower water ratios create high-strength concrete. A lesser amount leads to a denser microstructure. This denser structure provides better compressive strength but may be more difficult to work with.
- High Water-to-Cement Ratios: On the other hand, a higher ratio may enhance workability but compromises concrete strength. Excessive water weakens the mix, which might cause cracking and shrinkage in the cured product.
Moreover, it is important to establish balance. Finding that right ratio of water within the mixture leads to an ideal blend that possesses quality and resilience. Testing different ratios can help to find effective methods for particular situations in construction. The key remains to maintain the necessary hydration without excessive dilution.
It is crucial to always consider the moisture content of the materials. Pre-wet sand can alter how much water is needed in the mixture.
Physical Characteristics of the Mixture
The physical characteristics of the mixture of sand and cement play a critical role in determining its overall performance. It is essential to understand these characteristics to both utilize the mixture effectively in construction and achieve desired outcomes, such as strength, durability, workability, and finish.

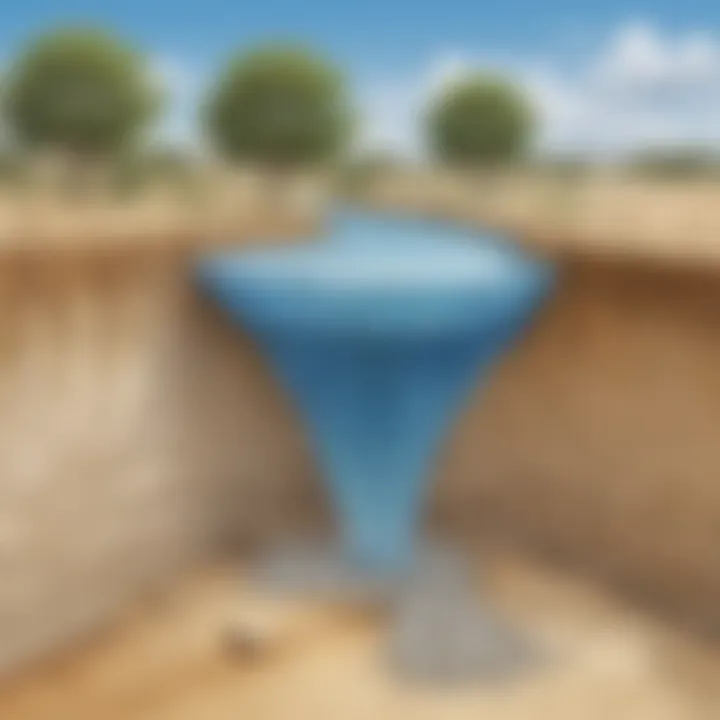
Strength and Durability
Strength refers to the ability of the material to withstand force without failing. In the context of sand and cement mixture, strength relies heavily on the curing process, the water-to-cement ratio, and various aggregates present outcome. As the combination the sand and cement dries, it solidifies into a hard mass, creating robust structures capable of supporting significant loads. When we discuss usability, it is crucial to maintain a proper balance. Overly high water content could lead to porosity, making concrete weak and prone to fracture. For optimum results, typically a w/c ratio of around 0.45 is recommended.
Durability, on the other hand, is about how well material can withstand environmental stressors over time. The inclusion of sand helps enhance concrete's overall resilience. Limitations in durability could lead to startling issues such as cracking and physical breakdown after exposure to harsh weather conditions. Research shows that the use of quality inputs such electricity defined sand improves durability abilities.
In general maintains the wow-factor of a solidly constructed building can stand for many decades.
While preparing concrete, using clean and well-graded sand ensures it bonds well with the cement. Unevenly sized aggregates can hamper the compactness, making durability a chief concern that practitioners must consider.
Workability and Finish
Workability reflects on how easy the concrete mixture can be manipulated during application. A mixture that is deemed too dry appears hard or difficult to mold and form while workability too fluid can lead to problems such deformities or discrepancy in the thickness of casts. Finding a balance is key.
To enhance workability, one might consider adding a plasticizer. This compound changes the properties of the mixture without compromising strength. The affability of the concrete matters especially during pours. Stop errors from occurring through improved workability guarantees straightened quality of work.
The finish, on the other hand, refers to the surface quality of the finished product. A smooth finish requires a lower proportion of water with added attention paid to work thickness and potential smooth assisting compounds during mixing project. Few exterior pathways require hide curves while promoting precise as it engages additional tied craftsmanship.
Through careful attention to both workability and finish, remarkable surfaces can be achieved, important for aesthetic appearances in projects, not only residential.google's influence in architecture.
When comparing early and late application of mixtures bear direct impact, it is noted that later mixes often experience improved ease in adjustement a minimal while workable situation adds to site productivity and worker satisfaction."
Common Applications of Sand and Cement Mixtures
Common applications of sand and cement mixtures are essential for effective construction and engineering processes. This section explores how these mixtures are utilized in everyday projects. Understanding these applications helps us appreciate why the right ratios and mixing techniques are so critical. Each use dictates specific property requirements that influence strength and durability. As we delve into this topic, consider how sand and cement interact to meet diverse structural needs.
Construction of Buildings
In building construction, sand and cement are the backbone of the structure. When mixed properly, they provide a strong foundation and support. The sand particles help with the distribution of weight and serve as a filler, while cement acts as the binding agent.
Some important considerations include:
- Weight Distribution: It is vital that the materials evenly spread the weight. If not, some parts might crack or fail under pressure.
- Load-Bearing Strength: The mixture’s ability to bear heavy weights feels the most strain from heavy artifacts, furniture, and occupants.
- Time to Cure: Buildings require a waiting period for the mixture to set and gain strength. This process must be well-managed to ensure quality work.
The construction industry continues to innovate in this area, developing new materials and improving existing products for better performance and sustainability.
Paving and Sidewalks
Paved surfaces create paths for vehicles and pedestrians. Sand and cement mixtures used in this context produce durable and aesthetically pleasing pavements. They resist weather conditions and heavy traffic, making them ideal for roads, driveways, and sidewalks.
Key points in this application include:
- Flexural Strength: Paving needs more flexible materials to endure bending without breaking.
- Durability: Resilience against harsh weather can prolong the lifespan of pavements significantly.
- Surface Finish: A smooth finish is crucial for usability and aesthetic appeal. Proper mixtures allow for fine finishes.
Ensuring the right mixture enables communities to have reliable, long-lasting surfaces for transit.
Mortar and Plastering
Mortar and plastering is another significant application of sand and cement mixtures, where they serve primarily decorative and functional purposes. Mortar is used to bond bricks and stones, while plaster provides a smooth finish to walls and ceilings. Quality control in these mixtures affects how well the materials perform.
Consider these elements:
- Wall Bond Strength: It needs to be adequately firm to retain structural integrity.
- Adhesion: Strong adhesion ensures plaster remains fixed to the underlying surface.
- Texture Quality: A smooth texture improves appearance and can help a space feel finished.
Mixing ratios may vary for these uses, often adjusted based on the project demands, which highlights the importance of precision in crafting these fundamental building materials.
Proper preparation and application of sand and cement mixtures can vastly improve quality and longevity in various construction projects.
Troubleshooting Mixture Problems
Addressing mixture problems is important in achieving a reliable sand and cement blend. Without proper troubleshooting, issues can lead to poor construction performance, increased costs, and safety risks. Through the examination of common issues and practical solutions, those involved in construction and craftsmanship can greatly enhance their outcomes. Understanding bthe challenges of mixing fosters a better approach to problem-solving and quality control.
Common Issues in Mixing
When mixing sand and cement, several problems may arise that affect the final product. Some frequent issues include:
- Inconsistent Texture: The mixture may even be too dry or too wet, impacting the workability.
- Clumping: Clumps can create weak spots in the structure, compromising integrity.
- Air Bubbles: Trapped air prevents optimal binding and strength.
- Settling Layers: Sometimes, layers can separate if not mixed thoroughly.
Observing these issues during the mixing process can provide insight to change before it's too late.
Solutions to Problems
Fortunately, most mixing issues have straightforward solutions. Here are key strategies to avoid and remedy these common problems:
- Achieve Consistency: Regularly check the water content and add consistently to have an ideal moisture level.
- Address Clumps Promptly: Use a mechanical mixer to break down clumps or manually agitate the mixture before final use.
- Eliminate Air Bubbles: Use proper agitation techniques to release trapped air. Compact layers when required.
- Thorough Mixing: Allow sufficient time in each mixing phase to ensure complete blending before considering the work done.
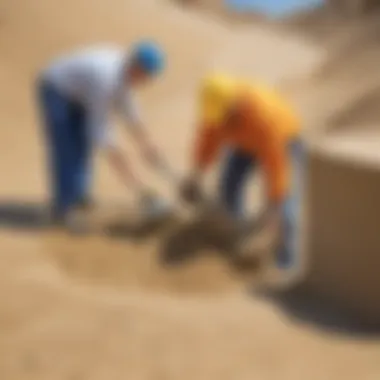
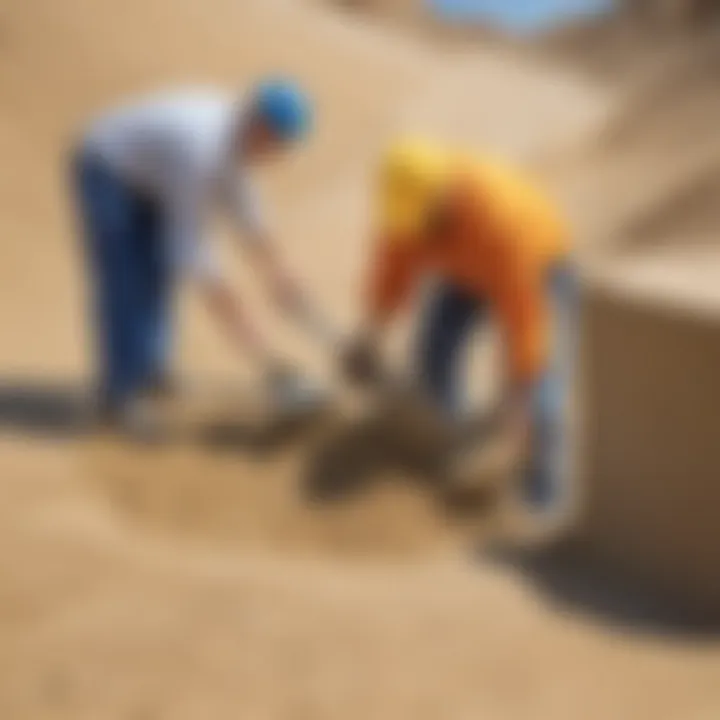
Implementing these solutions will not only improve the quality of the mixture but also enhance overall project efficiency.
"Quality in mix preparation leads to quality in final construction."
Through careful consideration of these elements, a more durable and reliable product will often result. This is essential, especially for projects backboning structural stability in varied constructions.
Environmental Considerations
The discussion around the mixture of sand and cement extends beyond just their engineering properties. Environmental considerations play a critical role, especially in an age where sustainability is increasingly important. Cement production is a significant source of carbon emissions. By understanding how to minimize the impact through responsible practices, we can help protect our planet while optimizing construction processes.
Sustainable Practices
Sustainable practices in the context of sand and cement mixtures mean using methods and materials that reduce environmental harm. Understanding which materials are sourced from environmentally friendly practices is key. For instance:
- Using Local Materials: Sourcing sand and aggregates locally reduces transportation emissions, saving fuel and minimizing the carbon footprint.
- Alternative Materials: Innovations like fly ash or slag can be used as partial substitutes for Portland cement. These materials repurpose waste, diminishing the overall ecological impact.
Incorporating these methods is not just good for the environment; it can also lead to cost savings and project efficiency.
Recycling Cement and Sand
Recycling cement and sand can tremendously lessen the demand for new materials. The process may include:
- Reusing Old Concrete: Old concrete can be crushed and repurposed as aggregates in new mixtures. This technique keeps materials in circulation and reduces quarrying impact.
- Adopting Circular Economy: Embracing a circular approach encourages using building materials in new constructions instead of discarding them, creating new opportunities in construction waste management.
The act of recycling not only conserves finite resources but also minimizes the volume of waste sent to landfills, supporting a healthier environment for future generations.
By implementing these strategies, we can make a compelling argument for the advantages of wise environmental considerations in construction, ensuring minimal impact on the earth while still enabling growth and infrastructure development.
Safety Precautions
Safety precautions are vital when working with sand and cement mixtures. Not only does this ensure the effectiveness of the construction materials, but it also safeguards the health of the personnel involved. Malpractices can lead to physical injuries or health issues. Therefore, understanding these precautions enhances safety and project quality.
Handling Materials Safely
Handling sand and cement requires attention and care. Workers must be educated on the proper lifting techniques. Always lift with your legs instead of your back to prevent strain or injury. Keep paths clear to avoid trips and falls, especially where materials are piled.
Moreover, maintain a clean work environment. Sweep up any spills quickly. Loose sand mix can create slippery areas, which leads to accidents. Mark all potential hazards. Create signage where necessary. Good visibility around work areas is essential.
While transporting these materials, use appropriate vehicles. Overloading can lead to accidents on the site. Ensure everyone knows the weight limits of equipment being used. Loading and unloading should be coordinated well to avoid mishaps.
Remember, safe practices benefit everyone, enhancing overall site productivity and morale.
Personal Protective Equipment
Personal Protective Equipment (PPE) is crucial in protecting workers. Essential gear includes gloves, masks, eye protection, and sturdy footwear. Wearing a dust mask, for instance, helps to prevent inhaling harmful particles when mixing. Dust emitted during mixing can lead to respiratory issues.
Eye protection is equally important. Small particles can easily get into the eyes and cause injuries. Safety goggles or glasses are recommend ways of shield for this risk.
The role of gloves cannot be understated. They protect hands from abrasions when handling rough materials. Also, they provide grip when dealing with wet mixes, which can be quite heavy and cumbersome. Lastly, sturdy footwear should be of non-slip nature to reduce slip and trip chances.
In summary, consistently using appropriate personal protective equipment minimizes risks, ensuring that the focus remains on the mixing and application processes rather than possible safety violations.
Future Trends in Sand and Cement Usage
The area of sand and cement usage is evolving as materials science evolves. The importance of this topic is becoming increasingly relevant due to global demands for sustainable construction materials. Environmental challenges prompt the industry to look for ways to improve material efficiency, make better use of resources, and reduce waste. Optimizing how sand and cement are mixed plays a big role in achieving stronger, more durable structures while considering environmental impacts.
Innovations in Material Science
Material science has driven efficiency in many epidemic building practices. Innovations include the introduction of new types of environmentally friendly cements and alternative binders. For instance, the development of geopolymer cement utilizes industrial by-products. These alternative cements are designed to have a lower carbon footprint compared to traditional Portland cement. They provide comparable results in strength while transitioning way younger climate protection methods.
Furthermore, researchers are exploring the use of recycled materials in the sand-cement mixtures. This is aimed at reducing the load on natural resources while still providing effective results in construction.
Another key innovation is in the area of additives. Incorporation of polymers or fibers can enhance the behavior of the mixture. These materials improve toughness and reduce cracking and thus promote long-lasting buildings. Innovations spanning into coatings and treatments have also proven beneficial.
Key benefits include:
- Lower material costs when utilizing waste materials
- Improved resistance to wear and tear
- Reduced water absorption
Impact of Technology on Mixing Techniques
Technology has revolutionized mixing techniques in construction. Advanced machinery allows for precise control of ratios during the mixing process. For example, volumetric mixer trucks provide accurate control over the drum outputs. This provides tons of benefits in actual construction sites.
Smart mixers that incorporate technology also allow monitoring of water content and consistency. This leads to improved workability of the final product. The inclusion of automated systems often reduces variability, which is important for ensuring structural integrity.
Cost efficiency is greatly leveraged. Crafting more effective and usable mixtures translates to savings not only in materials but also in time.
Significant impacts of these technologies include:
- Increased accuracy in mixing specifications
- Enhancement in speed of construction
- Consistency of final product properties
Emerging practices and technologies indicate where the construction industry may be headed. Innovations and tech-led improvements will continuously influence future changes in sand and cement usage.